Understanding the Injection Molding Process: A Comprehensive Guide
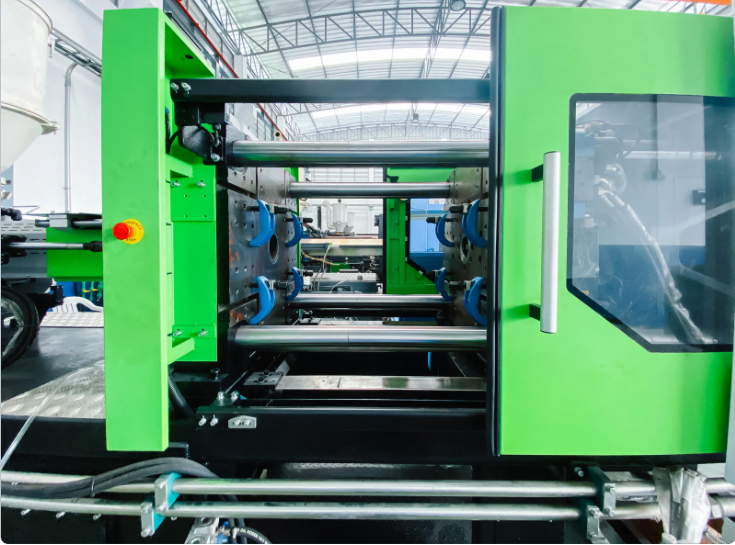
Introduction to Injection Molding
Injection molding is a widely used manufacturing process for producing parts by injecting molten material into a mold. This technique is particularly popular in the plastic industry due to its efficiency and ability to create complex shapes with high precision. In this article, we will delve into the injection molding process, its advantages, applications, and best practices for optimizing production.
What is Injection Molding?
Injection molding involves the following key steps:
- Material Preparation: Raw plastic pellets are fed into a hopper and heated until they melt.
- Injection: The molten plastic is injected into a mold cavity under high pressure.
- Cooling: The plastic cools and solidifies in the mold.
- Ejection: Once cooled, the mold opens, and the finished part is ejected.
This process allows for the rapid production of high-quality parts, making it ideal for industries such as automotive, consumer goods, and medical devices.
Benefits of Injection Molding
Injection molding offers numerous advantages, including:
- High Efficiency: The process allows for the rapid production of large quantities of parts.
- Precision: It produces parts with tight tolerances and intricate designs.
- Material Variety: A wide range of materials can be used, including thermoplastics, thermosets, and elastomers.
- Reduced Waste: The process minimizes material waste compared to traditional manufacturing methods.
Applications of Injection Molding
Injection molding is used in various industries, including:
- Automotive: Components such as dashboards, bumpers, and interior parts.
- Consumer Products: Items like containers, toys, and household appliances.
- Medical Devices: Syringes, surgical instruments, and diagnostic equipment.
- Electronics: Housings for gadgets and connectors.
Key Considerations for Injection Molding
Material Selection
Choosing the right material is crucial for the success of the injection molding process. Factors to consider include:
- Mechanical Properties: Strength, flexibility, and durability.
- Thermal Properties: Resistance to heat and temperature variations.
- Cost: Budget constraints and material availability.
Mold Design
A well-designed mold is essential for achieving high-quality parts. Key aspects include:
- Cavity Design: Ensuring the mold can accommodate the desired part shape.
- Cooling Channels: Designing efficient cooling systems to reduce cycle times.
- Ejection Mechanisms: Implementing effective methods for part removal.
Process Parameters
Optimizing process parameters can significantly impact production quality. Consider adjusting:
- Injection Speed: Balancing speed with material flow to prevent defects.
- Pressure: Maintaining adequate pressure to fill the mold completely.
- Temperature: Controlling melt and mold temperatures for optimal results.
Cost-Effective Production Strategies
To maximize efficiency and minimize costs in injection molding, consider the following strategies:
- Optimize Cycle Times: Analyze and reduce cycle times without compromising quality.
- Implement Automation: Use robotic systems for material handling and part ejection.
- Regular Maintenance: Ensure molds and machinery are well-maintained to prevent downtime.
Sustainability in Injection Molding
As industries shift towards more sustainable practices, injection molding is adapting in several ways:
- Recyclable Materials: Utilizing biodegradable and recyclable materials helps reduce environmental impact.
- Energy Efficiency: Implementing energy-efficient machinery can lower production costs and emissions.
- Waste Reduction: Adopting lean manufacturing principles minimizes waste throughout the production process.
Future Trends in Injection Molding
The injection molding industry is evolving, with several trends shaping its future:
- 3D Printing Integration: Combining 3D printing with injection molding for rapid prototyping and tooling.
- Smart Manufacturing: Utilizing IoT and data analytics to optimize production processes.
- Sustainable Practices: A growing focus on eco-friendly materials and processes.
Conclusion
Injection molding is a versatile and efficient manufacturing process that plays a crucial role in various industries. By understanding its intricacies and implementing best practices, businesses can optimize their production capabilities and stay competitive in the market.
Table: Key Characteristics of Injection Molding
Characteristic | Description |
---|---|
Efficiency | High-speed production of complex parts |
Material Variety | Wide range of materials available |
Precision | Tight tolerances and intricate designs |
Waste Reduction | Minimal material waste compared to other methods |
Applications | Automotive, consumer goods, medical devices |
Additional Resources
For more information on injection molding, consider exploring these links:
- Questions and Answers
- Opinion
- Motivational and Inspiring Story
- Technology
- True & Inspiring Quotes
- Live and Let live
- Focus
- Art
- Causes
- Crafts
- Dance
- Drinks
- Film/Movie
- Fitness
- Food
- Juegos
- Gardening
- Health
- Home
- Literature
- Music
- Networking
- Other
- Party
- Religion
- Shopping
- Sports
- Theater
- Wellness
- News
- Culture