Understanding the Difference Between Jacketed and Non-Jacketed Mixing Tanks
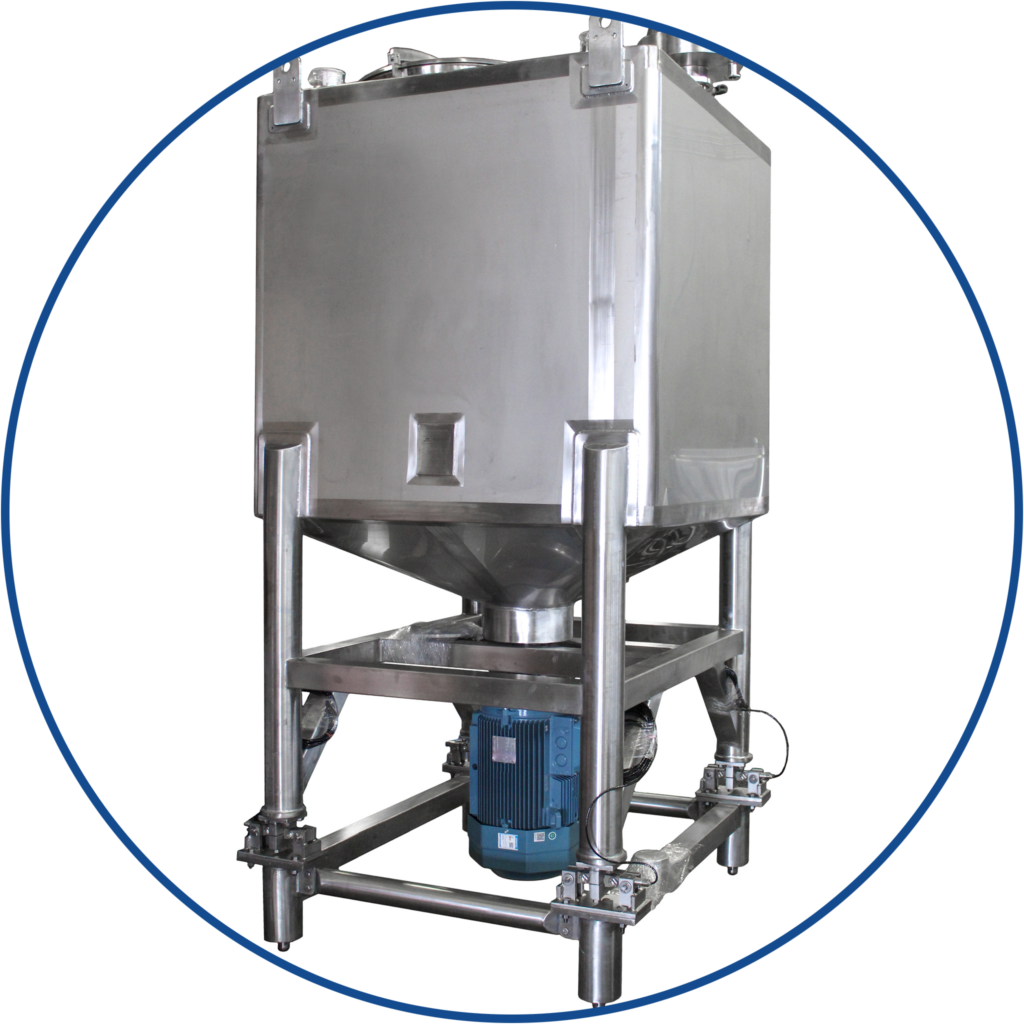
Mixing tanks are essential equipment in various industries, ranging from pharmaceuticals to food and beverage production. When it comes to selecting the right mixing tank for your specific application, one of the key decisions you will need to make is whether to choose a jacketed or non-jacketed tank. In this article, we will explore the differences between the two types of tanks and help you understand which option may be best suited for your needs.
What Are Jacketed Mixing Tanks?
Jacketed mixing tanks feature a secondary shell (jacket) that surrounds the main vessel. This jacket is designed to allow for the circulation of temperature-controlled fluids, such as water, steam, or glycol, to regulate the temperature of the contents inside the tank. This heating or cooling method is highly effective in maintaining precise temperature control during the mixing process, making jacketed tanks ideal for applications that require temperature-sensitive materials.
Advantages of Jacketed Mixing Tanks:
-
Precise temperature control
-
Uniform heating or cooling of contents
-
Ideal for temperature-sensitive materials
-
Reduced risk of hot spots or uneven distribution of heat
Disadvantages of Jacketed Mixing Tanks:
-
Higher initial cost due to the added complexity of the jacket
-
More maintenance and cleaning required for the jacketed system
-
Limited heat transfer capabilities compared to non-jacketed tanks
What Are Non-Jacketed Mixing Tanks?
Non-jacketed mixing tanks, on the other hand, do not have a secondary shell surrounding the main vessel. Instead, these tanks rely on external methods, such as external heat exchangers or direct steam injection, to heat or cool the contents inside. While non-jacketed tanks may not offer the same level of temperature control as jacketed tanks, they are often more cost-effective and easier to maintain.
Advantages of Non-Jacketed Mixing Tanks:
-
Lower initial cost compared to jacketed tanks
-
Simpler design with fewer components
-
Easier cleaning and maintenance
-
Higher heat transfer capabilities for faster processing
Disadvantages of Non-Jacketed Mixing Tanks:
-
Limited temperature control compared to jacketed tanks
-
Greater risk of hot spots or uneven heating
-
Not suitable for temperature-sensitive materials
Which Type of Mixing Tank Is Right for You?
When deciding between a jacketed and non-jacketed mixing tank, it is essential to consider the specific requirements of your application. If you need precise temperature control and are working with temperature-sensitive materials, a jacketed tank may be the best option for you. On the other hand, if cost-effectiveness and ease of maintenance are your top priorities, a non-jacketed tank may be more suitable.
In conclusion, understanding the differences between jacketed and non-jacketed mixing tanks is crucial in selecting the right equipment for your processing needs. Whether you prioritize temperature control, cost-effectiveness, or ease of maintenance, there is a mixing tank out there that can meet your requirements. By carefully considering your specific application and requirements, you can make an informed decision that will help you achieve optimal results in your mixing processes.
- Questions and Answers
- Opinion
- Motivational and Inspiring Story
- Technology
- True & Inspiring Quotes
- Live and Let live
- Focus
- Art
- Causes
- Crafts
- Dance
- Drinks
- Film/Movie
- Fitness
- Food
- Games
- Gardening
- Health
- Home
- Literature
- Music
- Networking
- Other
- Party
- Religion
- Shopping
- Sports
- Theater
- Wellness
- News
- Culture