Step-by-Step Guide to Conducting Root Cause Analysis During Audits
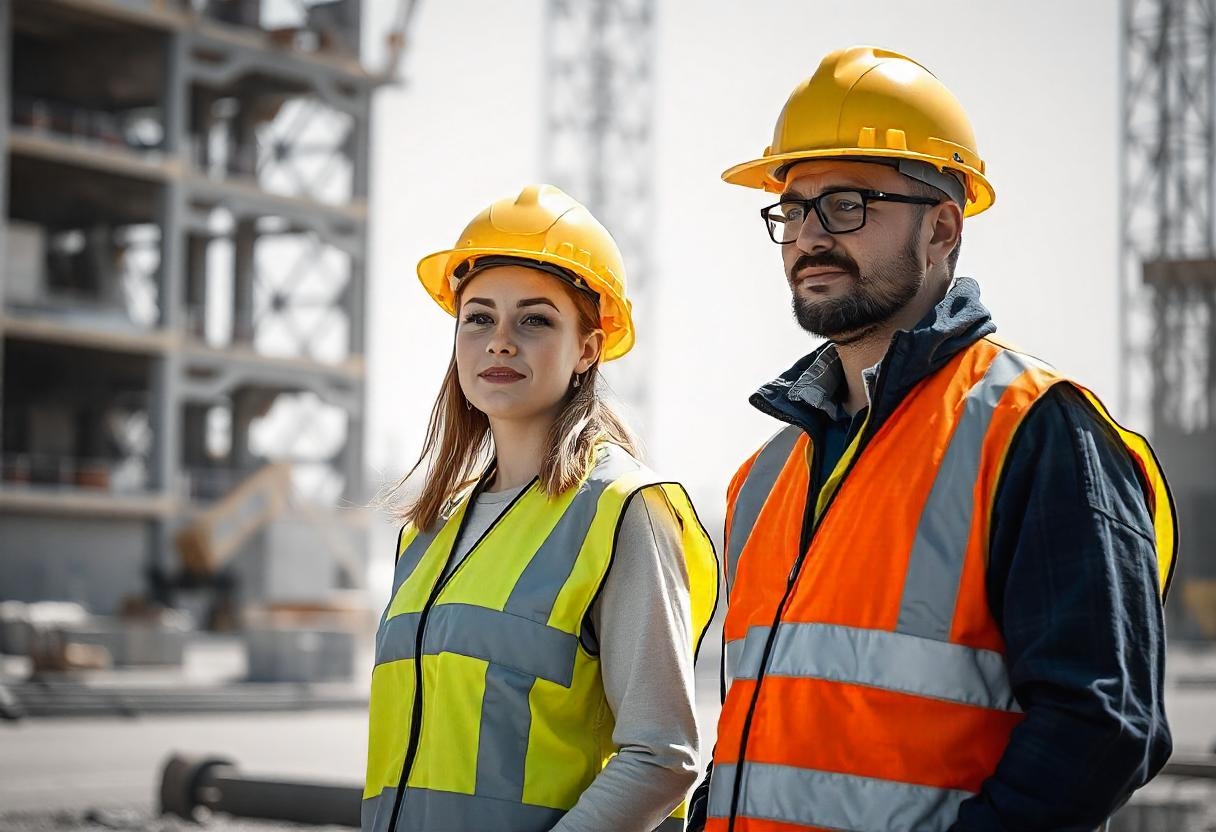
Conducting an audit in any workplace is essential to identify hazards and ensure safety measures are effective. However, discovering a problem during an audit is only the beginning. The key to truly improving workplace safety is understanding why the problem happened in the first place. This is where root cause analysis comes in. In this article, we'll walk you through a straightforward, step-by-step guide to conducting root cause analysis during audits, helping you tackle hazards at their source and build a safer working environment.
What is Root Cause Analysis?
Before we dive into the steps, let’s clarify what root cause analysis means. It’s a method used to identify the fundamental reason behind a problem or hazard. Instead of just fixing the surface issue, root cause analysis digs deeper to uncover what caused it. For example, if workers are frequently slipping in a warehouse, the root cause might be poor floor maintenance rather than just wet spots on the floor.
Root cause analysis is vital in workplace hazard management because it helps prevent the same problem from recurring. Fixing only the symptoms wastes resources and puts employees at continued risk.
Why Root Cause Analysis Matters in Workplace Audits
During audits, safety professionals might find hazards like blocked emergency exits, malfunctioning equipment, or chemical spills. Addressing these issues immediately is necessary, but understanding why these hazards exist helps stop them permanently.
For example, if emergency exits are blocked repeatedly, a root cause analysis might reveal poor storage practices or inadequate training rather than careless behavior. By targeting the root causes, organizations can reduce workplace accidents, improve compliance, and even lower their insurance costs.
A Quick Note About NEBOSH Course Fees and Safety Training
Before we start, it’s important to highlight how NEBOSH course fees relate to improving safety practices like root cause analysis. Investing in NEBOSH courses equips professionals with the knowledge to conduct effective audits and root cause analyses. These internationally recognized courses cover a wide range of workplace hazards, preparing you to tackle issues confidently.
While the NEBOSH course fee might seem like an upfront investment, it pays off by helping you prevent costly accidents and compliance fines in the long run.
Step-by-Step Guide to Conducting Root Cause Analysis During Audits
Step 1: Identify the Problem Clearly
The first step is to describe the problem precisely. During an audit, you might note a hazard or unsafe condition. Instead of vague statements like "equipment is faulty," specify exactly what is wrong: "the conveyor belt stops unexpectedly every 10 minutes."
Write down all observations carefully. Clear problem definition helps focus the investigation and avoids confusion later.
Step 2: Gather Data and Evidence
Next, collect as much information as possible. This might include:
-
Photographs of the hazard
-
Maintenance logs
-
Employee interviews
-
Safety incident reports
For example, if a chemical spill happened, check records of chemical storage, staff training, and past incidents. The goal is to understand the situation fully before guessing the cause.
Step 3: Ask “Why?” Repeatedly (The 5 Whys Technique)
One popular root cause analysis tool is the 5 Whys technique. Keep asking why the problem occurred, each time digging deeper. For example:
-
Why was the chemical spilled?
Because the container was not sealed properly. -
Why was it not sealed properly?
Because the staff didn’t know how to seal it. -
Why didn’t they know?
Because they weren’t trained properly. -
Why wasn’t training provided?
Because of a lack of training schedule. -
Why is there no training schedule?
Because no one was assigned to manage training.
Here, the root cause might be the lack of a dedicated training coordinator.
Step 4: Use Fishbone Diagrams to Visualize Causes
Sometimes, multiple factors cause a problem. A Fishbone Diagram (or Ishikawa diagram) helps categorize causes visually under headings like People, Process, Equipment, Environment, and Materials.
For example, when investigating frequent slips, causes might include:
-
People: inadequate footwear
-
Process: poor cleaning schedule
-
Equipment: faulty floor mats
-
Environment: wet weather conditions
This method helps audit teams see all potential causes clearly.
Step 5: Validate the Root Cause
Once you think you have the root cause, test it. Discuss findings with your team or employees familiar with the process. Sometimes, additional evidence or insights emerge that refine your understanding.
Validation prevents misdiagnosis that could lead to ineffective fixes.
Step 6: Develop Action Plans
After confirming the root cause, create an action plan to eliminate it. This could involve:
-
Training programs
-
Process changes
-
Equipment maintenance or replacement
-
Improved safety protocols
Make sure actions are realistic, assigned to responsible people, and have deadlines.
Step 7: Monitor and Review
Root cause analysis doesn’t end with implementing fixes. Continuously monitor the situation to ensure the problem doesn’t return. Regular audits and feedback loops are vital for long-term safety improvement.
An Anecdote to Illustrate Root Cause Analysis
Let me share a real-world story to highlight the importance of root cause analysis.
At a manufacturing plant, workers kept getting minor burns near a heating machine. Management tried several quick fixes—adding warning signs, giving workers gloves—but burns continued.
During an audit, the safety officer used root cause analysis. They discovered the gloves provided were too thick to allow proper machine handling, causing workers to take shortcuts. Further, the machine's temperature controls were hard to see and adjust.
By replacing gloves with thinner, heat-resistant ones and improving machine controls, the burns stopped. The root cause wasn’t just the hazard but also poor equipment design and protective gear.
How Root Cause Analysis Supports Hazard Management
The process we outlined fits perfectly into broader hazard management strategies. Root cause analysis:
-
Improves workplace safety by addressing problems at their source
-
Helps comply with legal and industry safety standards
-
Reduces costs from repeated accidents and downtime
-
Builds a proactive safety culture
Auditors and safety officers who master root cause analysis become valuable assets for their organizations.
Frequently Asked Questions about Root Cause Analysis in Audits
What tools are best for root cause analysis?
Popular tools include the 5 Whys technique, Fishbone diagrams, and Failure Mode and Effects Analysis (FMEA). Choose the one that fits your audit’s complexity.
Can root cause analysis be applied to all workplace hazards?
Yes! From slips and trips to chemical exposure and equipment failure, root cause analysis helps uncover underlying causes for any hazard.
How often should root cause analysis be performed?
It should be part of every safety audit and incident investigation to continuously improve safety measures.
For more details, read about the NEBOSH Fee in Pakistan and how it fits into your professional development plans.
Why You Should Buy a Root Cause Analysis Product or Service
If you’re serious about workplace safety, investing in a good root cause analysis software or training product can be a game-changer. These tools guide you through the process, organize data efficiently, and help teams collaborate better.
They also provide templates, reports, and reminders so nothing gets missed. Plus, having digital evidence ready can simplify compliance audits.
With the right product, you’ll reduce human error, speed up investigations, and build safer workplaces confidently.
Final Thoughts
Root cause analysis during audits is not just a box to tick but a powerful tool that transforms how you manage workplace hazards. By following the step-by-step guide, you can uncover hidden causes, implement effective solutions, and prevent hazards from recurring.
Remember, investing in your knowledge through courses like NEBOSH—and using the right tools—makes this process easier and more impactful. Ultimately, safer workplaces protect your people, your reputation, and your bottom line.
- Questions and Answers
- Opinion
- Motivational and Inspiring Story
- Technology
- True & Inspiring Quotes
- Live and Let live
- Focus
- Art
- Causes
- Crafts
- Dance
- Drinks
- Film/Movie
- Fitness
- Food
- Игры
- Gardening
- Health
- Главная
- Literature
- Music
- Networking
- Другое
- Party
- Religion
- Shopping
- Sports
- Theater
- Wellness
- News
- Culture