How Fluid Mixers & Slurry Plants Improve Construction Efficiency
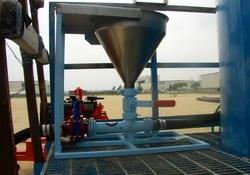
In modern construction, especially in trenchless technology and underground infrastructure projects, efficiency and precision are key to completing tasks on time and within budget. Among the essential equipment that significantly contribute to construction efficiency are Fluid Mixers & Slurry Plants. These specialized systems play a crucial role in preparing and managing slurry, a mixture of water, bentonite, polymers, and other additives, used to facilitate excavation, stabilize boreholes, and ensure smooth operation of drilling and boring equipment.
This article explores how Fluid Mixers & Slurry Plants enhance construction efficiency by improving material consistency, reducing downtime, promoting environmental safety, and enabling faster project completion.
The Role of Fluid Mixers & Slurry Plants in Construction
Before understanding their impact on efficiency, it’s important to grasp what Fluid Mixers & Slurry Plants are and their function. These systems mix and maintain slurry—a thick, viscous fluid used during horizontal directional drilling (HDD), microtunneling, and other trenchless methods—to cool and lubricate cutting tools, transport drill cuttings to the surface, and stabilize borehole walls.
Fluid Mixers are responsible for blending bentonite, polymers, water, and other additives into a homogenous slurry mixture. They typically include high-speed mixers, agitators, and storage tanks.
Slurry Plants are larger, integrated setups that not only mix slurry but also recycle and treat it to separate solids and reuse water, minimizing environmental impact and conserving resources.
How Fluid Mixers & Slurry Plants Improve Construction Efficiency
1. Consistent and High-Quality Slurry Production
One of the main advantages of using advanced Fluid Mixers & Slurry Plants is their ability to produce slurry with consistent properties. Maintaining the correct slurry density, viscosity, and chemical composition is critical for effective drilling.
-
Efficiency Impact: Consistent slurry reduces equipment wear, prevents borehole collapse, and enhances the transport of cuttings to the surface. This reduces the risk of machine jams and delays, allowing drilling operations to proceed smoothly.
-
How It Works: Fluid mixers use precision control systems to measure and mix components accurately, ensuring the slurry meets project specifications every time. Continuous agitation prevents settling or separation of particles.
2. Reduced Downtime Through Effective Slurry Management
Construction projects face costly downtime when equipment fails or operations stall. Poorly managed slurry can clog pumps, wear out pipes, and damage drilling equipment.
-
Efficiency Impact: Well-managed slurry systems minimize downtime by preventing these issues. Slurry plants that include recycling units remove solids and restore slurry quality, enabling prolonged use of the same fluid without frequent replacement.
-
How It Works: Slurry treatment processes such as settling tanks, centrifuges, and hydrocyclones separate solids from slurry, allowing clean slurry to be recirculated. This not only extends equipment life but also reduces the need for new slurry preparation.
3. Faster Project Completion and Reduced Operating Costs
By improving slurry quality and reducing downtime, Fluid Mixers & Slurry Plants contribute directly to faster project timelines.
-
Efficiency Impact: Projects that rely on trenchless construction benefit from continuous drilling with minimal interruptions. This efficiency translates to lower labor and equipment rental costs, ultimately reducing the total project budget.
-
How It Works: Optimized slurry preparation and recycling allow operators to maintain a steady workflow. The ability to adjust slurry properties on-the-fly using control panels ensures operators can respond to changing ground conditions without stopping work.
4. Environmental Benefits and Regulatory Compliance
Efficient slurry plants not only enhance construction operations but also reduce environmental impact, which is increasingly important due to stricter regulations.
-
Efficiency Impact: Minimizing slurry waste and water consumption lowers disposal costs and environmental fines, creating smoother project approvals and fewer regulatory delays.
-
How It Works: Recycling slurry reduces water usage and prevents contaminated slurry discharge. Modern plants incorporate filtration and treatment stages to meet environmental standards, enabling sustainable construction practices.
5. Enhanced Safety on Construction Sites
Proper slurry handling also plays a role in maintaining safe working conditions.
-
Efficiency Impact: Well-maintained slurry systems prevent unexpected equipment failures and hazardous spills. This improves overall site safety and reduces accident-related delays.
-
How It Works: Automated monitoring systems in slurry plants track pressure, flow, and slurry composition, alerting operators to potential problems before they escalate.
Practical Examples of Efficiency Gains
-
In horizontal directional drilling, fluid mixers provide stable slurry that prevents borehole collapse when drilling under roads and waterways, reducing the risk of costly repairs and rework.
-
In microtunneling, slurry plants enable continuous operations by recycling bentonite slurry used for lubrication and soil stabilization, reducing downtime and conserving resources.
-
During pipeline installations, consistent slurry produced by fluid mixers ensures smooth pipe jacking, avoiding friction issues that could delay progress.
Selecting the Right Fluid Mixers & Slurry Plants for Efficiency
To maximize these benefits, construction firms must carefully select fluid mixers and slurry plants suited to their project’s scale and soil conditions.
-
Capacity and Flexibility: Larger projects require slurry plants with higher capacity and multi-stage treatment to handle variable soil loads.
-
Automation and Control: Advanced control systems simplify operation and improve responsiveness.
-
Mobility: Portable slurry plants offer flexibility for projects in remote or urban locations.
-
Maintenance: Easy-to-maintain designs reduce downtime for repairs and cleaning.
Conclusion
Fluid Mixers & Slurry Plants are fundamental to enhancing construction efficiency in trenchless and underground projects. By ensuring consistent slurry quality, reducing equipment downtime, promoting environmental responsibility, and improving safety, these systems allow contractors to complete projects faster and more cost-effectively.
- Questions and Answers
- Opinion
- Motivational and Inspiring Story
- Technology
- True & Inspiring Quotes
- Live and Let live
- Focus
- Geopolitics
- Military-Arms/Equipment
- Sicurezza
- Economy/Economic
- Art
- Causes
- Crafts
- Dance
- Drinks
- Film/Movie
- Fitness
- Food
- Giochi
- Gardening
- Health
- Home
- Literature
- Music
- Networking
- Altre informazioni
- Party
- Religion
- Shopping
- Sports
- Theater
- Health and Wellness
- News
- Culture