Choosing the Right Rivet Nut for Industrial Use
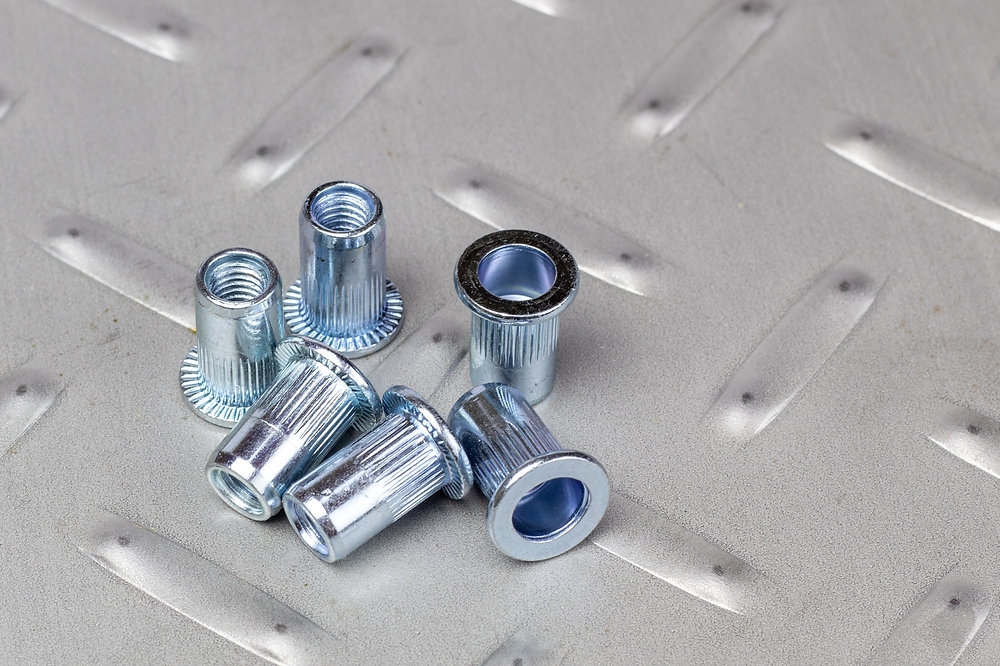
In the world of industrial manufacturing and assembly, the choice of fastening solutions can make or break the integrity and efficiency of a project. One such essential fastener is the rivet nut—a versatile component used across automotive, aerospace, electronics, and construction industries. At STANLEY, we understand the importance of choosing the right rivet nut for the job. This article will guide you through the different types of rivet nuts and how to select the most suitable one for your industrial application.
What is a Rivet Nut?
A rivet nut, also known as a rivnut or threaded insert, is a mechanical fastener designed to provide a strong threaded connection in thin materials such as sheet metal, plastic, or composite panels. Installed from one side of a workpiece (blind installation), rivet nuts are ideal where the reverse side is inaccessible.
Unlike traditional nuts and bolts, rivet nuts do not require tapping or welding, making them a go-to solution for many engineers looking for efficiency, reliability, and durability.
Types of Rivet Nuts
Choosing the right rivet nut begins with understanding the available types and their intended uses. STANLEY offers a wide variety of rivet nuts tailored for specific industrial needs.
-
Round Body Rivet Nuts
These are the most common rivet nuts and come in smooth or knurled variants. Knurled bodies provide better grip in softer materials like plastic or aluminum, while smooth bodies are ideal for harder surfaces. -
Hex Body Rivet Nuts
Designed to resist spinning after installation, hex body rivet nuts are ideal for applications requiring high torque. They are best used in hexagonal holes for maximum resistance. -
Slotted Rivet Nuts
Featuring a slotted body that collapses during installation, these are ideal for soft or thin materials. The collapsed sections provide a large backside footprint, distributing load evenly. -
Sealed Rivet Nuts
Used in environments where moisture or gas resistance is important. They have a closed-end design to prevent contaminants from entering the thread. -
Large Flange vs. Small Flange Rivet Nuts
Large flange rivet nuts offer greater load-bearing surface, which helps distribute stress, while small flange versions are more compact and flush with the surface, ideal for space-constrained areas.
Key Considerations When Choosing a Rivet Nut
Selecting the right rivet nut involves evaluating several critical factors:
1. Material Compatibility
Rivet nuts are available in steel, stainless steel, aluminum, and brass. For corrosion resistance, stainless steel or aluminum may be preferred, especially in marine or outdoor environments. Steel rivet nuts are ideal for applications demanding high strength.
2. Load Requirements
Determine the shear and tensile loads the fastener needs to handle. A heavy-duty application like an automotive chassis demands stronger materials and larger sizes than a consumer electronics panel.
3. Installation Environment
Will the rivet nut be exposed to high temperatures, chemicals, or moisture? Choose materials and coatings (e.g., zinc-plated, passivated) that can withstand these conditions.
4. Access to Installation Site
Rivet nuts are especially useful for blind installation. If only one side of the material is accessible, they offer a significant advantage over traditional fastening methods.
5. Installation Tools
Rivet nuts can be installed using manual hand tools, pneumatic guns, or automated systems. Choosing the right installation equipment ensures the fastener is properly seated and secured.
STANLEY's Commitment to Quality and Innovation
At STANLEY, we combine decades of fastening innovation with engineering expertise to deliver rivet nut solutions that meet the highest industry standards. Our broad product line includes standard and custom rivet nuts designed for superior performance in demanding environments.
We also offer application engineering support, helping manufacturers select, test, and implement the best fastening solution. Whether you’re securing aluminum panels on an aircraft or assembling an electronics enclosure, STANLEY has the right rivet nut for the job.
Conclusion
Choosing the right rivet nut is crucial for achieving long-lasting, secure, and efficient assemblies in industrial applications. From understanding the types and materials to evaluating your specific use case, every decision impacts the strength and reliability of the final product. STANLEY’s wide selection of rivet nuts and industry-leading support ensure that your fastening needs are met with precision and confidence.
For more information or to speak with a fastening expert, contact STANLEY today—your trusted partner in industrial fastening solutions.
- Questions and Answers
- Opinion
- Motivational and Inspiring Story
- Technology
- True & Inspiring Quotes
- Live and Let live
- Focus
- Art
- Causes
- Crafts
- Dance
- Drinks
- Film/Movie
- Fitness
- Food
- Spellen
- Gardening
- Health
- Home
- Literature
- Music
- Networking
- Other
- Party
- Religion
- Shopping
- Sports
- Theater
- Wellness
- News
- Culture