Can laser welding stainless steel really replace traditional methods in precision-critical industries?
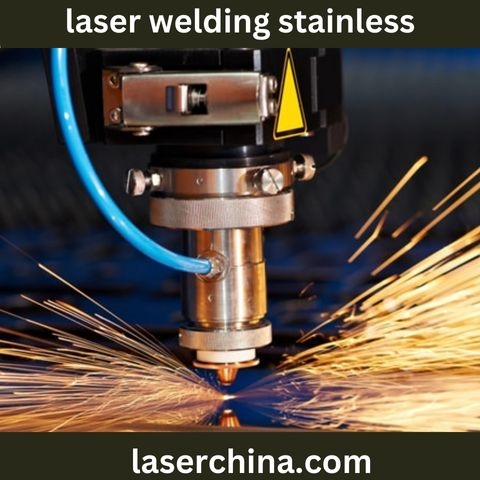
When discussing the cutting-edge methods of joining metal materials, especially in industries where precision, strength, and appearance matter, one phrase frequently comes up: laser welding stainless. But can this technique truly outpace traditional welding methods and dominate high-precision sectors such as aerospace, medical manufacturing, or electronics?
To answer that, we need to unpack what laser welding stainless steel truly involves, how it integrates with modern manufacturing standards, and why it has become a go-to solution for industry leaders around the world.
Understanding the Core Process
Laser welding stainless steel is not just a welding process — it's a transformation in how metallic bonds are created. Using a highly concentrated beam of light, the technique focuses thermal energy with such precision that it melts the stainless steel exactly where needed. Unlike arc welding, which relies on a broader area of heat application, the laser approach allows pinpoint control over the depth and width of the weld.
This is particularly valuable when working with stainless steel, a material known for its resilience, corrosion resistance, and frequent use in demanding environments. The integrity of stainless steel can be compromised by excessive heat input or contamination during welding, making laser welding a smart alternative. The minimal heat-affected zone (HAZ) ensures that the metallurgical properties of stainless remain intact while still producing clean, strong welds.
Industry-Specific Precision and Control
Laser welding stainless steel has found immense application in industries where absolute precision is non-negotiable. Let’s take a closer look at a few sectors that rely heavily on this process:
1. Medical Device Manufacturing
From surgical tools to implantable devices, medical instruments require ultra-clean welds with no room for contamination. Laser welding stainless meets this demand due to its contactless nature and exceptional cleanliness. It creates hermetically sealed joints which prevent bacterial ingress — a critical need in devices like pacemakers or stainless surgical instruments.
2. Aerospace and Defense
Aircraft and satellite components must endure extreme stress, vibration, and environmental conditions. Precision is crucial, and traditional welding methods often leave behind imperfections that become points of failure. The laser beam’s controlled depth and focus ensure welds are consistent, with deep penetration and minimal warping — especially on thin stainless steel panels used in fuselage structures or turbine housings.
3. Electronics and Battery Production
In battery enclosures, sensor housings, and microelectronic devices, even the smallest distortion or spatter can render a component unusable. Here, laser welding stainless excels due to its ability to work on micron-scale welds. It enables automation on a production line without sacrificing accuracy, ensuring product longevity and performance.
A Shift in Production Philosophy
What’s driving manufacturers toward laser welding stainless steel isn’t just precision — it’s a complete shift in production ideology. In the past, welding was often seen as a “post-fabrication” process, something added after a component had been formed. But with laser welding, the line between design and production is blurred. Engineers now design with the weld in mind, knowing that laser technology allows them to push boundaries.
Complex geometries once considered too risky to weld are now fair game. Designers can include intricate channels, curved seams, or multi-material joints because laser systems can adapt with robotic or CNC-assisted heads. This flexibility opens up innovation in design that conventional methods simply can’t match.
Surface Integrity and Cosmetic Appeal
In consumer-facing industries, appearance is everything. Think of stainless steel in kitchen appliances, high-end cutlery, or automotive trim. These surfaces need flawless finishes. One of the silent strengths of laser welding stainless lies in its ability to produce visually clean seams — often requiring no post-weld polishing or grinding. The aesthetic weld lines not only reduce production time but also enhance the final product's visual appeal.
Automation Integration and Cost Efficiency
There’s a misconception that laser welding stainless is expensive and exclusive to large-scale operations. In reality, technological advancements have made these systems more accessible. Whether in a small fabrication shop or a large automotive production line, laser welders can be integrated with automation systems like robotic arms, vision-guided weld heads, or conveyor-based laser cells.
This automation not only reduces labor costs but also drastically improves repeatability. Once the weld parameters are dialed in, every weld is identical, which reduces rework and enhances consistency — a crucial metric in quality control environments.
Weld Strength and Microstructure Control
Delving into metallurgy, laser welding influences the microstructure of stainless steel in unique ways. The high cooling rates associated with the laser process can refine the grain structure of the weld, enhancing its mechanical properties. This is critical for load-bearing components or items exposed to temperature fluctuation and corrosion.
Because laser welding stainless generates such a narrow fusion zone, it minimizes the risk of chromium carbide precipitation — a common issue in conventional welding that can lead to corrosion along the grain boundaries. By preserving the material's corrosion resistance, laser welds extend the operational life of the component.
Environmental and Energy Efficiency
With growing emphasis on green manufacturing, laser welding stainless also offers an eco-conscious advantage. It consumes less energy than arc-based systems and produces minimal waste, smoke, or by-products. The process often requires no filler material, flux, or shielding gases in high-vacuum environments, making it cleaner and more environmentally responsible.
Additionally, the precision of the laser reduces scrap rates. Fewer rejections mean less material waste and a more sustainable production cycle. This aligns with the growing global standards in manufacturing ESG (Environmental, Social, Governance) compliance.
Safety and Operational Simplicity
One might assume that such a high-tech process would require intense operator training. While it’s true that laser systems demand initial setup expertise, once configured, they offer one of the safest and most consistent operational experiences in welding. Enclosed workstations, automated shut-offs, and built-in monitoring systems make laser welding stations safer than traditional arc or TIG welding setups.
Real-World Implementation Examples
To illustrate the practicality of laser welding stainless, consider a manufacturer of stainless steel kitchen sinks. With laser technology, they can weld the sink bowl to the top panel with an almost invisible seam, eliminating the need for extensive polishing. The result? A premium product with a streamlined finish — at scale.
In another example, a battery manufacturer uses laser welding for stainless casings, achieving both speed and leak-tightness for lithium-ion cell packs used in electric vehicles. The process allows them to scale production while maintaining strict safety and performance standards.
Final Thoughts
The evolution of manufacturing has always been about pushing boundaries: tighter tolerances, cleaner processes, and greater design freedom. Laser welding stainless is a powerful contributor to this evolution. It replaces bulk with precision, unpredictability with control, and post-processing with seamless integration.
Whether you’re manufacturing surgical instruments, crafting aesthetic consumer products, or building the next generation of electric vehicles, embracing laser welding stainless steel means stepping into a future where quality, performance, and innovation come together — not as an option, but as a standard.
- Questions and Answers
- Opinion
- Motivational and Inspiring Story
- Technology
- True & Inspiring Quotes
- Live and Let live
- Focus
- Geopolitics
- Military-Arms/Equipment
- Security
- Economy/Economic
- Art
- Causes
- Crafts
- Dance
- Drinks
- Film/Movie
- Fitness
- Food
- Games
- Gardening
- Health
- Home
- Literature
- Music
- Networking
- Other
- Party
- Religion
- Shopping
- Sports
- Theater
- Health and Wellness
- News
- Culture