DTF Transfers: The Future of Custom Printing
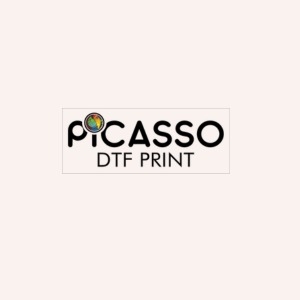
The world of custom printing is rapidly evolving, and DTF (Direct-to-Film) transfers have emerged as one of the most exciting and efficient technologies in the industry. Whether you're a business looking to offer custom apparel, a creative individual working on a DIY project, or an entrepreneur launching a print-on-demand store, DTF transfers offer a modern, cost-effective solution that’s versatile, fast, and reliable.
In this article, we’ll explore what DTF transfers are, how they work, and why they’re becoming a popular choice for custom printing, particularly in the apparel and promotional products markets.
What Are DTF Transfers
DTF transfer stands for Direct-to-Film transfer. This method involves printing a design onto a special film and then transferring that design onto fabric or other materials using heat and pressure. Unlike other printing techniques, such as screen printing or Direct-to-Garment (DTG) printing, DTF allows for printing on a variety of surfaces, including both light and dark fabrics.
DTF transfer printing has gained popularity because it doesn’t require the extensive setup of traditional methods, offers high-quality results, and is relatively easy to scale for both small and large orders. With the ability to print intricate designs and vibrant colors, DTF technology is becoming a game-changer for custom print providers and businesses in the apparel, home goods, and promotional products industries.
How Does DTF Transfer Work
DTF transfer involves several key steps, each playing a vital role in achieving high-quality, durable prints. Here’s a breakdown of how the process works:
1. Design Creation
The process begins with creating the design in graphic design software like Adobe Illustrator or Photoshop. This design can range from logos and text to more intricate artwork, depending on the needs of the customer. Once the design is ready, it’s saved in a digital format that is compatible with the DTF printer.
2. Printing onto Transfer Film
The design is then printed onto a special PET film using a DTF printer. DTF printers use CMYK inks (cyan, magenta, yellow, and black) to print full-color designs, and white ink is used to ensure the design stands out on dark fabrics. The white ink layer acts as a base, providing opacity and vibrancy to designs on darker materials.
3. Applying Adhesive Powder
Once the design is printed, an adhesive powder is applied to the film while the ink is still wet. The powder sticks to the printed ink, and the film is then placed into a curing oven or heat press to melt and cure the adhesive. This step ensures that the design will adhere properly when transferred to the fabric.
4. Heat Press Transfer
Finally, the transfer film is placed onto the fabric, and a heat press is used to apply heat and pressure. This activates the adhesive, bonding the design permanently to the fabric. After pressing, the film is peeled away, leaving behind a high-quality, durable print that’s resistant to fading, cracking, and peeling—even after multiple washes.
Why Are DTF Transfers Gaining Popularity
DTF transfers technology is rapidly becoming a preferred method in custom printing for several reasons. Here’s why it’s gaining traction:
1. Versatility Across Materials
DTF transfer can be used on a wide range of materials, including cotton, polyester, cotton-poly blends, and even non-fabric materials such as wood, leather, and ceramics. This gives print providers the flexibility to create a broad range of products, from t-shirts and hoodies to custom promotional items and home décor.
2. High-Quality, Vibrant Prints
The combination of CMYK inks and white ink allows DTF transfers to produce sharp, vibrant, and detailed prints. The colors are rich, and the design quality is high, making it ideal for intricate or multi-colored artwork. The use of a white ink underlay on dark fabrics ensures that designs pop, even on challenging colors.
3. Durable and Long-Lasting
DTF prints are known for their durability. The designs are permanently bonded to the fabric, making them resistant to fading, peeling, and cracking. This makes DTF ideal for apparel that will see frequent use and washing, such as custom t-shirts, sportswear, or uniforms. The print maintains its integrity over time, ensuring that your custom products look great even after multiple washes.
4. Cost-Effective for Small Runs
Unlike screen printing, which requires expensive setup costs and is best for large orders, DTF transfer is cost-effective for small print runs. The process doesn’t require separate screens or plates for each color, which means there are no setup fees for each individual print. This makes it an affordable solution for businesses that need to produce small batches of custom designs quickly and efficiently.
5. No Pre-Treatment Required
Unlike DTG printing, which often requires pre-treatment of fabrics (especially dark ones), DTF transfers don’t require pre-treatment. This simplifies the workflow and reduces production time, making DTF printing faster and more convenient.
6. Quick Turnaround Time
The DTF process is relatively fast compared to traditional methods. Once the design is created, the printing, powder application, curing, and heat pressing steps can be completed in a relatively short amount of time. This makes DTF transfer an excellent choice for businesses that need to fulfill quick turnaround orders or meet tight deadlines.
DTF Transfer vs. Other Printing Methods
To truly understand the advantages of DTF transfer, let’s compare it to some other common printing methods:
-
DTF vs. Screen Printing:
- Screen printing is best suited for large runs but can be costly for smaller orders due to the setup process. DTF, on the other hand, is more cost-effective for small orders and doesn’t require the creation of separate screens for each color. This makes DTF ideal for print-on-demand businesses or customers who need custom designs in small quantities.
-
DTF vs. DTG Printing:
- DTG (Direct-to-Garment) printing is great for printing detailed designs directly onto cotton fabrics, but it often requires pre-treatment and is generally slower and more expensive than DTF. DTF doesn’t require pre-treatment, works on both light and dark fabrics, and can print on a broader range of materials, making it more versatile.
-
DTF vs. Sublimation:
- Sublimation printing is best for printing on polyester fabrics and works only with light-colored materials. DTF printing, however, can be used on both light and dark fabrics, including cotton, polyester, and more, providing more flexibility in terms of fabric choices.
Conclusion
DTF transfers are transforming the world of custom printing, offering businesses and individuals a flexible, cost-effective, and high-quality method for creating custom designs on a wide range of materials. Whether you’re running a small business that offers custom apparel, a hobbyist creating personalized products, or an entrepreneur launching a print-on-demand store, DTF technology provides a fast and efficient way to bring your ideas to life.
- Questions and Answers
- Opinion
- Motivational and Inspiring Story
- Technology
- True & Inspiring Quotes
- Live and Let live
- Focus
- Art
- Causes
- Crafts
- Dance
- Drinks
- Film/Movie
- Fitness
- Food
- Jogos
- Gardening
- Health
- Início
- Literature
- Music
- Networking
- Outro
- Party
- Religion
- Shopping
- Sports
- Theater
- Wellness
- News
- Culture