Straightening Machines: A Comprehensive Guide
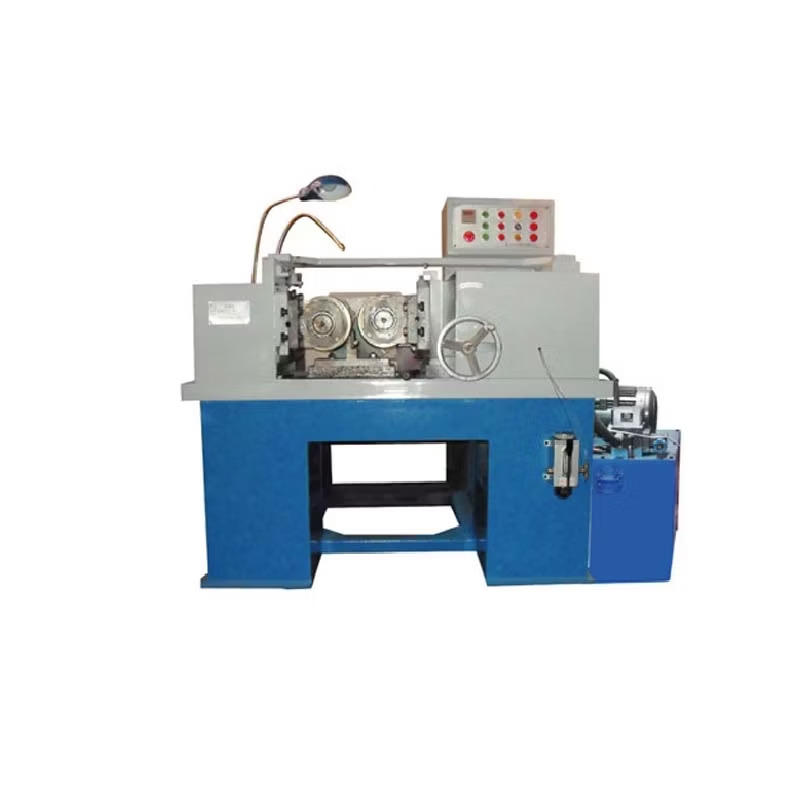
Straightening machines are vital in many industries, offering precision and efficiency in processing materials. These machines play a crucial role in shaping, flattening, or aligning various materials such as metal, wire, tubes, or sheets. This article provides a detailed exploration of straightening machines, their types, working principles, applications, and benefits, catering to industries that depend on these indispensable tools.
What Are Straightening Machines?
Straightening machines are specialized mechanical devices designed to correct the alignment of materials. They are commonly used in manufacturing processes to straighten bent, deformed, or uneven materials, ensuring uniformity and accuracy.
The primary function of straightening machines is to deliver materials with precise geometrical properties. This uniformity is essential for industries like construction, automotive, aerospace, and metal fabrication, where the quality and shape of materials are critical.
Types of Straightening Machines
Straightening machines come in various types to address specific industry needs. Below are the most common ones:
1. Roller Straightening Machines
Roller Straightening machines are the most widely used. They feature multiple rollers arranged in a series, which apply pressure to the material, correcting any deformations. These machines are ideal for straightening sheets, wires, and long metallic objects.
2. Bar Straightening Machines
These machines are specifically designed for straightening metal bars, rods, and pipes. Bar straightening machines use a combination of rollers and rotating mechanisms to eliminate bends and kinks from the material.
3. Wire Straightening Machines
Wire straightening machines are designed to handle thin and flexible wires. These machines use rollers or dies to straighten the wires without causing damage to their surface.
4. Tube Straightening Machines
These machines are used to straighten tubular materials, ensuring the uniformity of hollow sections like pipes and tubes. Tube straightening machines are widely employed in industries such as plumbing, automotive, and construction.
How Do Straightening Machines Work?
Straightening machines operate based on principles of mechanical force and alignment. Here is a breakdown of their working process:
1. Material Feeding
The material is fed into the machine, either manually or automatically. Feeding mechanisms ensure the material enters the machine at the correct angle.
2. Roller Alignment
The machine's rollers are aligned to create pressure points along the material's length. These pressure points gradually remove bends or deformations.
3. Compression and Tension
The rollers apply compression and tension to the material, reshaping it to achieve straightness. The amount of force applied is carefully calibrated to avoid overcorrection or damage.
4. Final Adjustment
The straightened material is subjected to a final adjustment phase, ensuring precision and uniformity. Advanced machines use sensors and monitoring systems to detect deviations and make corrections in real time.
Applications of Straightening Machines
Straightening machines are indispensable in industries where material accuracy and consistency are paramount. Some common applications include:
1. Metal Fabrication
In metal fabrication, straightening machines are used to prepare raw materials for welding, cutting, and assembling processes.
2. Automotive Industry
The automotive sector relies on straightening machines to process components like chassis parts, axles, and rods.
3. Construction
Construction projects use straightening machines to ensure the precision of steel bars, beams, and sheets used in structural frameworks.
4. Wire Manufacturing
Wire straightening machines are essential in producing electrical wires, cables, and fencing materials.
5. Pipeline Construction
Tube straightening machines play a critical role in the pipeline industry, ensuring pipes meet stringent alignment standards.
Benefits of Straightening Machines
The use of straightening machines offers several advantages:
1. Improved Material Quality
Straightening machines enhance the quality of materials by removing imperfections and irregularities, resulting in a smooth and uniform finish.
2. Increased Efficiency
By automating the straightening process, these machines reduce manual labor and speed up production, increasing overall efficiency.
3. Cost Savings
Improved material accuracy minimizes waste and reduces the need for rework, leading to significant cost savings for manufacturers.
4. Versatility
Straightening machines can handle a wide range of materials, making them versatile tools for various industrial applications.
5. Consistency and Precision
Modern straightening machines are equipped with advanced technology that ensures consistent and precise results, meeting the high standards required by many industries.
Choosing the Right Straightening Machine
Selecting the right straightening machine depends on several factors:
1. Material Type
Consider the type of material to be straightened, such as metal sheets, bars, wires, or tubes.
2. Material Dimensions
The machine should be capable of handling the material's dimensions, including thickness, diameter, and length.
3. Production Volume
For high-volume production, opt for machines with automation features to maximize efficiency.
4. Accuracy Requirements
Industries with stringent accuracy requirements should invest in machines equipped with advanced monitoring and control systems.
5. Budget Constraints
Balance your budget with the features and capabilities of the machine to find the best fit for your needs.
Maintenance of Straightening Machines
Regular maintenance is crucial to ensure the longevity and performance of straightening machines. Here are some tips for maintaining these machines:
-
Routine Inspections: Conduct regular inspections to identify and address wear and tear on rollers and other components.
-
Lubrication: Keep moving parts well-lubricated to reduce friction and prevent damage.
-
Calibration: Periodically calibrate the machine to maintain accuracy and precision.
-
Cleaning: Remove debris and residue from the machine to prevent blockages and maintain smooth operation.
-
Professional Servicing: Schedule professional maintenance to address complex issues and replace worn-out components.
Innovations in Straightening Machines
The latest advancements in straightening machines have significantly enhanced their capabilities. Some notable innovations include:
-
Automation: Modern straightening machines are equipped with automated feeding and adjustment systems for seamless operation.
-
Sensor Technology: Advanced sensors monitor material alignment and detect deviations, enabling real-time corrections.
-
Energy Efficiency: Energy-efficient machines reduce power consumption and contribute to sustainable manufacturing practices.
-
Customizability: Many machines can be customized to meet specific industrial requirements, offering greater flexibility.
Conclusion
Straightening machines are essential tools in industrial processes, ensuring materials meet high-quality standards. From roller straightening machines to specialized wire and tube straightening machines, their versatility and efficiency make them invaluable across multiple industries.
Whether you’re in construction, automotive, or metal fabrication, investing in the right straightening machine can improve product quality, enhance efficiency, and reduce operational costs. By understanding the types, applications, and benefits of straightening machines, industries can make informed decisions to optimize their manufacturing processes.
- Questions and Answers
- Opinion
- Motivational and Inspiring Story
- Technology
- True & Inspiring Quotes
- Live and Let live
- Focus
- Art
- Causes
- Crafts
- Dance
- Drinks
- Film/Movie
- Fitness
- Food
- Juegos
- Gardening
- Health
- Home
- Literature
- Music
- Networking
- Other
- Party
- Religion
- Shopping
- Sports
- Theater
- Wellness
- News
- Culture