Ammonium Nitrate Production Cost: Market and Key Factors
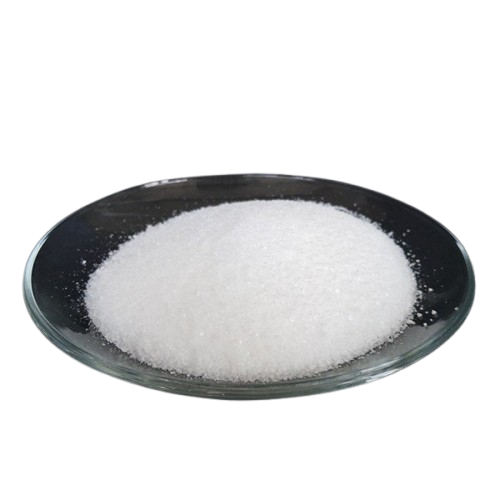
Ammonium nitrate (NH₄NO₃) is a key chemical compound used in various applications, most notably in fertilizers, explosives, and even in the production of certain industrial chemicals. It plays a crucial role in the agriculture industry as a nitrogen fertilizer, contributing significantly to global food production. In the explosives industry, ammonium nitrate production cost analysis is used in the manufacturing of explosives for mining, construction, and demolition purposes. Understanding the cost structure involved in ammonium nitrate production is crucial for manufacturers, suppliers, and industries that rely on this compound.
This article delves into the critical cost components involved in the production of ammonium nitrate, from raw material procurement and energy consumption to labor costs, technological innovation, and regulatory factors. We will also provide insights into market trends and future projections for ammonium nitrate prices.
Request a Free Sample For Ammonium Nitrate Production Cost Reports - https://www.
Key Factors Influencing Ammonium Nitrate Production Costs
The production of ammonium nitrate is an energy-intensive and complex chemical process that involves several key stages, including the production of ammonia, nitration, neutralization, and drying. Each stage has its associated costs, which ultimately contribute to the overall production cost. Let’s examine the primary factors affecting ammonium nitrate production:
1. Raw Material Costs
The raw materials used in ammonium nitrate production primarily include ammonia (NH₃) and nitric acid (HNO₃). These materials contribute significantly to the overall production cost.
-
Ammonia (NH₃): Ammonia is the most critical raw material in ammonium nitrate production, accounting for around 60-70% of the final product’s cost. Ammonia is typically produced via the Haber-Bosch process, which combines nitrogen (from air) and hydrogen (from natural gas or other feedstocks) at high temperatures and pressures. The cost of ammonia is heavily dependent on natural gas prices, as natural gas is the primary feedstock for hydrogen production. Therefore, fluctuations in natural gas prices directly affect ammonia costs, which in turn impacts the cost of ammonium nitrate production.
-
Nitric Acid (HNO₃): Nitric acid is another essential raw material for ammonium nitrate production, accounting for approximately 20-30% of production costs. Nitric acid is typically produced by oxidizing ammonia, and its production cost is influenced by factors such as raw material prices, energy costs, and the technology used in the manufacturing process.
-
Other Chemicals and Additives: Depending on the specific requirements for the end-product, other chemicals and additives (such as stabilizers or anti-caking agents) may be used during the production of ammonium nitrate, adding to the overall raw material costs.
Read Full Report - https://www.
2. Energy Costs
Ammonium nitrate production is an energy-intensive process. The major energy-consuming stages include the production of ammonia (via the Haber-Bosch process) and the nitric acid production process, both of which require large amounts of heat and electricity.
-
Ammonia Production: The Haber-Bosch process, used to synthesize ammonia, consumes significant amounts of natural gas, both as a raw material and as a source of energy. The efficiency of the ammonia synthesis plant and fluctuations in natural gas prices have a substantial impact on production costs.
-
Nitric Acid Production: The oxidation of ammonia to produce nitric acid also requires considerable energy, typically in the form of high-temperature combustion. The cost of energy (whether natural gas, electricity, or other fuels) directly influences the overall cost of ammonium nitrate production.
-
Drying Process: The final stage in ammonium nitrate production involves the drying and granulation of the product, which consumes additional energy. Energy costs for drying are typically influenced by fuel prices and the efficiency of drying equipment.
3. Labor and Operational Costs
Labor costs are an important factor in ammonium nitrate production, particularly in plants that are labour-intensive or lack automation. These costs are influenced by several factors:
-
Skilled Labor: Ammonium nitrate production requires skilled personnel, particularly in areas such as plant operation, safety monitoring, quality control, and maintenance. Highly trained workers are needed to ensure the safe and efficient operation of chemical plants, as ammonium nitrate is a potentially hazardous compound.
-
Health and Safety Measures: Due to the hazardous nature of ammonium nitrate (which can be explosive under certain conditions), strict safety regulations must be adhered to in production facilities. These safety measures require investments in protective equipment, safety training, and emergency preparedness, which add to labor costs.
-
Automation: Larger, more automated plants may reduce labor costs per unit of output. However, smaller plants or older facilities that rely more heavily on manual labor typically face higher operational costs.
4. Technological Advancements and Process Efficiency
Technological advancements in ammonium nitrate production can significantly impact overall production costs, especially by improving energy efficiency and reducing raw material wastage.
-
Energy-Efficient Equipment: The use of energy-efficient technologies in ammonia synthesis, nitric acid production, and drying can reduce energy consumption, which is one of the most significant cost components. Modern catalytic processes, improved heat recovery systems, and the use of renewable energy sources are all contributing factors to reducing energy costs in ammonium nitrate production.
-
Process Integration: Some manufacturers use integrated production processes, where ammonia and nitric acid are produced in a way that minimizes energy waste. For example, the energy produced during ammonia production can be used to fuel nitric acid synthesis, improving overall plant efficiency and reducing costs.
-
Automation and Monitoring: Advanced monitoring systems and automated processes can reduce labor costs, improve production efficiency, and lower the risk of costly accidents or production delays. Automated systems are particularly important for maintaining consistent product quality and ensuring safety standards are met.
5. Environmental and Regulatory Costs
Ammonium nitrate production is subject to stringent environmental regulations due to its potential environmental impact. Governments across the globe have enacted policies and regulations to ensure that ammonium nitrate production is carried out safely and with minimal harm to the environment.
-
Emissions Regulations: Ammonium nitrate plants must comply with emissions standards, particularly for nitrogen oxides (NOx), carbon dioxide (CO₂), and particulate matter. Compliance with these regulations often requires the installation of pollution control equipment, such as scrubbers and filters, which adds to production costs.
-
Safety Regulations: Due to the hazardous nature of ammonium nitrate, production facilities must comply with stringent safety regulations to prevent accidents such as explosions. This can involve the installation of specialized safety equipment, regular safety training, and the maintenance of emergency response systems. The costs of maintaining such safety protocols can be significant.
-
Waste Management: The production of ammonium nitrate generates waste, including by-products and materials that may require special disposal methods. Regulatory requirements for waste disposal and recycling can add to operational costs.
Ask an Analyst -https://www.
6. Transportation and Distribution Costs
Transportation and distribution costs are another important component of ammonium nitrate production costs. Given the bulk nature of the product and its potential hazards, transportation can be expensive.
-
Logistics and Delivery: Ammonium nitrate must be transported in bulk, often by truck, rail, or ship, to end users such as fertilizer manufacturers or mining companies. The distance between the production facility and customers, along with fuel costs and transportation infrastructure, impacts overall distribution costs.
-
Packaging: For small-scale applications, ammonium nitrate may need to be packaged, which adds costs for packaging materials, labor, and storage.
Market Outlook and Price Forecast (2024-2032)
The global ammonium nitrate market is influenced by several factors, including the demand from the agriculture and explosives industries, raw material costs, and energy prices. Given the volatility in natural gas prices and growing concerns over environmental regulations, the price trajectory of ammonium nitrate is expected to fluctuate in the coming years.
Short-Term Outlook (2024-2026)
In the short term, ammonium nitrate prices are expected to be influenced by:
-
Energy Price Fluctuations: Rising natural gas prices may lead to higher ammonia production costs, thus pushing ammonium nitrate prices higher.
-
Demand from Agriculture and Mining: As global agricultural and mining activities recover post-pandemic, demand for ammonium nitrate as a fertilizer and explosive is expected to rise.
Price Range (2024-2026): Ammonium nitrate prices may fluctuate between.
Medium-Term Outlook (2027-2029)
In the medium term, factors such as technological advancements in energy efficiency and the increased adoption of sustainable practices in chemical production may lead to price stabilization. However, regulatory pressures on emissions and safety standards may continue to add costs.
Price Range (2027-2029): Prices may range, depending on global energy and regulatory conditions.
Long-Term Outlook (2030-2032)
The long-term outlook for ammonium nitrate prices will depend on:
-
Technological Innovation: Further advancements in production technology, particularly in energy efficiency and waste minimization, may help stabilize prices.
-
Environmental and Regulatory Impact: Stricter environmental regulations could lead to higher compliance costs, especially for older facilities that need to upgrade equipment to meet emissions standards.
Request a Free Sample -https://www.
Contact Us:
Company Name: Procurement Resource
Contact Person: Leo Frank
Email: sales@procurementresource.com
Toll-Free Numbers:
- USA & Canada: +1 307 363 1045
- UK: +44 7537171117
- Asia-Pacific (APAC): +91 1203185500
Address: 30 North Gould Street, Sheridan, WY 82801, USA
- Questions and Answers
- Opinion
- Motivational and Inspiring Story
- Technology
- True & Inspiring Quotes
- Live and Let live
- Focus
- Geopolitics
- Military-Arms/Equipment
- Art
- Causes
- Crafts
- Dance
- Drinks
- Film/Movie
- Fitness
- Food
- Games
- Gardening
- Health
- Home
- Literature
- Music
- Networking
- Other
- Party
- Religion
- Shopping
- Sports
- Theater
- Wellness
- News
- Culture