Magnesium Antimonate Manufacturing Plant Project Report 2025: Process, Market and Sustainability
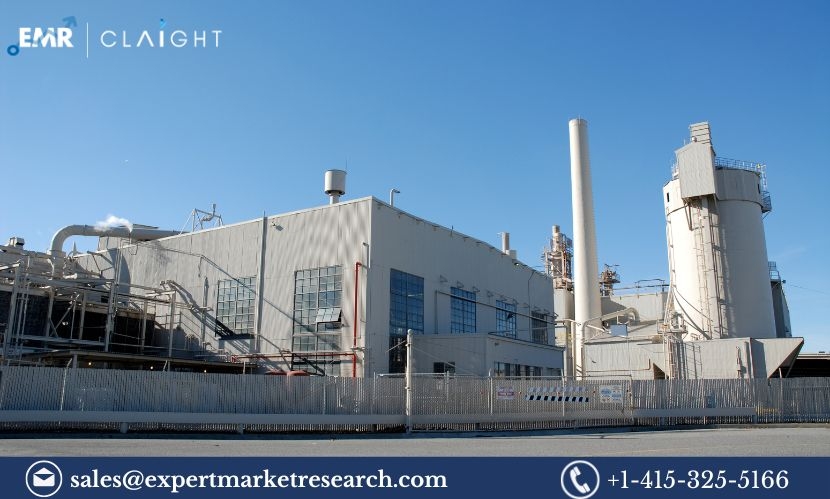
Introduction
The Magnesium Antimonate Manufacturing Plant Project Report provides a detailed overview of the processes, market analysis, technical aspects, and financial planning involved in establishing a plant for the production of magnesium antimonate (MgSbO₃). Magnesium antimonate is a compound that has specialized applications in various industries, particularly in electronics, ceramics, and fireproofing materials. This report explores the fundamental components required for the successful establishment of a magnesium antimonate manufacturing facility, including market demand, raw materials, production methods, plant design, cost analysis, and safety considerations.
Market Overview
Magnesium antimonate is widely used for its flame-retardant properties, high thermal stability, and electrical conductivity. It is particularly beneficial in industries where these attributes are highly valued, such as in the manufacture of fire-resistant materials, ceramics, electronics, and specialty coatings. As industries focus more on high-performance materials that meet stringent safety and environmental standards, the demand for magnesium antimonate continues to grow.
Key Market Drivers:
- Flame Retardant Industry: Magnesium antimonate is used as an effective flame retardant in various materials, including plastics and textiles. The increasing need for fireproof materials in construction and manufacturing is driving the demand for magnesium antimonate.
- Electronics and Semiconductors: Due to its electrical conductivity and high thermal resistance, magnesium antimonate finds applications in electronics, especially in semiconductors and circuit boards.
- Ceramics and Glass Industry: The compound is used in the formulation of specialty ceramics, where its thermal stability and chemical properties are highly advantageous.
- Environmentally Friendly Materials: As industries move towards sustainable and non-toxic materials, magnesium antimonate offers an eco-friendly alternative to some other flame retardants.
Get a Free Sample Report with Table of Contents@
Raw Materials and Sourcing
The primary raw materials for the production of magnesium antimonate include magnesium oxide (MgO), antimony trioxide (Sb₂O₃), and water. These raw materials are readily available from global suppliers. The sourcing and procurement of high-quality magnesium oxide and antimony trioxide are critical to ensure the consistency and purity of the final product.
Key Raw Materials:
- Magnesium Oxide (MgO): Sourced from magnesite or dolomite, magnesium oxide serves as the source of magnesium in the production of magnesium antimonate.
- Antimony Trioxide (Sb₂O₃): Antimony trioxide is the main precursor for the antimony component of magnesium antimonate. It is sourced from antimony ores.
- Water: Used as a solvent during the synthesis process.
Manufacturing Process
The production of magnesium antimonate follows a straightforward chemical reaction between magnesium oxide and antimony trioxide in the presence of water. The process typically involves the following steps:
1. Preparation of Reactants:
- Magnesium oxide is ground into a fine powder and mixed with water to create a suspension or slurry.
- Antimony trioxide is also prepared by grinding and dissolving it into the slurry.
2. Chemical Reaction:
- The magnesium oxide slurry is then combined with antimony trioxide in a reaction vessel. This mixture undergoes a controlled reaction where magnesium antimonate (MgSbO₃) is formed.
- The reaction is typically carried out at moderate temperatures to ensure complete conversion.
3. Precipitation and Separation:
- The magnesium antimonate is precipitated out of the reaction mixture. The solid product is separated from the liquid phase using filtration or centrifugation.
4. Drying:
- The magnesium antimonate is dried in vacuum or rotary dryers to remove any remaining moisture, resulting in a fine, dry powder.
5. Packaging:
- After drying, the magnesium antimonate is packaged in sealed containers or bags for distribution to end-users in industries such as flame retardants, ceramics, and electronics.
Plant Design and Layout
A magnesium antimonate manufacturing plant requires a specialized design to accommodate the various stages of production, from raw material storage to product packaging. Below are the key components of plant design:
Key Design Considerations:
-
Raw Material Storage:
- Magnesium oxide and antimony trioxide should be stored in dry, temperature-controlled environments to prevent degradation and ensure consistent quality.
-
Reaction Vessel:
- The plant will require reactors or vessels made from corrosion-resistant materials, as the reaction involves potentially hazardous chemicals.
-
Filtration and Separation Equipment:
- Filtration units or centrifuges will be necessary to separate the magnesium antimonate from the liquid phase. These systems must be designed for high efficiency and minimal contamination.
-
Drying Equipment:
- Dryers such as rotary dryers or vacuum dryers are essential for removing moisture from the precipitated product.
-
Quality Control Laboratory:
- A quality control lab should be established to test raw materials, intermediates, and the final product to ensure they meet industry specifications and quality standards.
-
Waste Management and Environmental Controls:
- Proper waste treatment facilities must be in place to handle any byproducts and emissions from the production process. This includes systems for solid waste disposal and air filtration to comply with environmental regulations.
-
Safety Systems:
- Given the use of chemicals and high temperatures, stringent safety protocols, including fire suppression systems and gas detection systems, must be implemented to protect workers and the facility.
Financial Planning
Establishing a magnesium antimonate manufacturing plant requires significant investment, both for initial setup and ongoing operations. Below are the key financial considerations:
Initial Capital Investment:
- Land and Facility Construction:
- The cost of acquiring land and constructing the plant facility will be one of the largest capital expenditures. The facility should be located in an industrial zone with easy access to transportation networks and raw material suppliers.
- Machinery and Equipment:
- Investment in specialized reaction vessels, filtration systems, drying equipment, and quality control labs is necessary for production.
- Licensing and Permits:
- Obtaining the necessary permits for construction, health and safety, environmental compliance, and chemical handling will incur additional costs.
Operating Costs:
- Raw Material Costs:
- The cost of magnesium oxide and antimony trioxide will make up a significant portion of operating expenses. These materials should be procured from reliable suppliers to ensure consistent quality and pricing.
- Energy Costs:
- Energy consumption will be high due to the heating and drying processes involved in magnesium antimonate production. Energy-efficient machinery and systems will help reduce these costs over time.
- Labor Costs:
- Skilled labor is essential for operating the plant, managing production, and ensuring safety compliance. Labor costs will include both direct workers and supervisory staff.
- Maintenance Costs:
- Regular maintenance of production equipment, safety systems, and quality control labs is necessary to ensure the smooth operation of the plant.
Revenue Generation:
- Revenue will primarily come from the sale of magnesium antimonate to industries such as flame retardants, electronics, and ceramics. Customization of the product to meet specific industry needs, such as high-purity grades for electronics, can help command premium prices.
Profitability:
- With optimized production processes, strong market demand, and effective cost management, the plant can achieve profitability within a few years. Expanding into global markets and diversifying product offerings will further boost the plant's profitability.
Regulatory Compliance
Given the nature of the raw materials and chemicals involved, regulatory compliance is essential for the successful operation of the magnesium antimonate manufacturing plant.
- Environmental Regulations:
- The plant must adhere to local and international environmental standards regarding emissions, water usage, and waste disposal.
- Health and Safety Regulations:
- Compliance with health and safety regulations, such as worker protection standards and hazardous chemical handling protocols, is critical. Personal protective equipment (PPE) and emergency response plans should be in place.
- Quality Control Standards:
- Ensuring the final product meets ISO and industry-specific standards for purity and performance will be vital to gaining customer trust and maintaining market competitiveness.
Marketing and Distribution Strategy
To effectively market magnesium antimonate, the following strategies should be considered:
-
Brand Positioning:
- Position magnesium antimonate as a high-performance, eco-friendly flame retardant and material for various industrial applications.
-
Target Market:
- The target markets include flame retardant manufacturers, electronics companies, ceramic manufacturers, and specialty coatings suppliers.
-
Distribution Channels:
- Establish relationships with distributors and wholesalers in the target industries. International trade partnerships can help expand market reach and open new avenues for growth.
FAQ
1. What is magnesium antimonate used for?
Magnesium antimonate is used primarily as a flame retardant, as well as in electronics, ceramics, and specialty coatings due to its thermal stability and electrical conductivity.
2. How is magnesium antimonate produced?
It is produced by reacting magnesium oxide with antimony trioxide in water, followed by filtration, drying, and packaging.
3. What industries use magnesium antimonate?
Industries such as flame retardants, electronics, ceramics, specialty coatings, and construction use magnesium antimonate in their manufacturing processes.
4. What are the key raw materials for magnesium antimonate production?
The key raw materials are magnesium oxide, antimony trioxide, and water.
5. Is the demand for magnesium antimonate increasing?
Yes, the demand is growing due to its application in high-performance materials, including fire-resistant products and specialty coatings.
Media Contact:
Company Name: Claight Corporation
Contact Person: Lewis Fernandas, Corporate Sales Specialist — U.S.A.
Email: sales@expertmarketresearch.com
Toll Free Number: +1–415–325–5166 | +44–702–402–5790
Address: 30 North Gould Street, Sheridan, WY 82801, USA
Website: www.expertmarketresearch.com
Aus Site: https://www.expertmarketresearch.com.au
- Questions and Answers
- Opinion
- Motivational and Inspiring Story
- Technology
- True & Inspiring Quotes
- Live and Let live
- Focus
- Geopolitics
- Military-Arms/Equipment
- Art
- Causes
- Crafts
- Dance
- Drinks
- Film/Movie
- Fitness
- Food
- Games
- Gardening
- Health
- Home
- Literature
- Music
- Networking
- Other
- Party
- Religion
- Shopping
- Sports
- Theater
- Wellness
- News
- Culture