Creatine Monohydrate Manufacturing Plant Project Report 2025: Technical, Financial, and Operational Insights
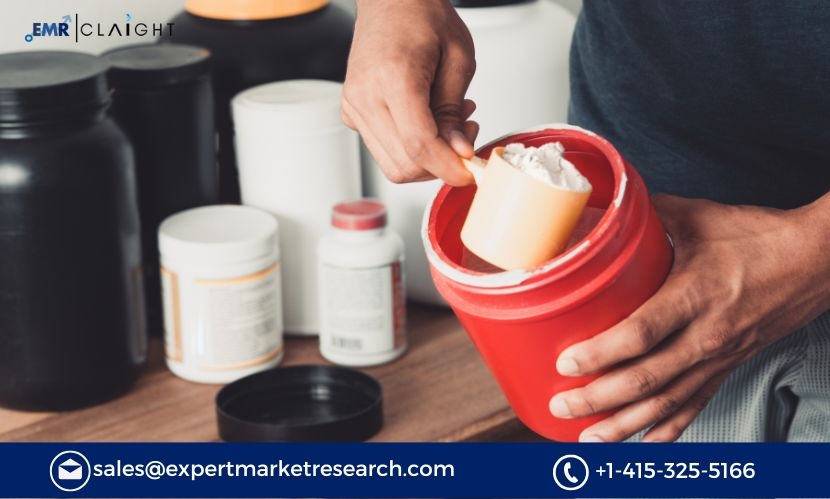
Introduction
Creatine Monohydrate is one of the most widely used and researched dietary supplements globally, primarily consumed by athletes, bodybuilders, and fitness enthusiasts to improve strength, endurance, and overall performance. It is naturally found in the human body and in foods such as meat and fish, and is commonly taken in supplement form to increase muscle mass, enhance strength, and improve high-intensity exercise performance. With the growing global awareness of health and fitness, the demand for sports nutrition products, particularly creatine-based supplements, has increased significantly. Establishing a Creatine Monohydrate Manufacturing Plant presents a lucrative business opportunity to meet this rising demand. This Creatine Monohydrate Manufacturing Plant Project Report aims to provide a detailed analysis of setting up such a manufacturing facility, covering essential factors such as market trends, raw materials, production processes, cost analysis, and regulatory requirements.
Market Demand and Trends
The global sports nutrition market has been expanding rapidly, with creatine supplements holding a dominant position due to their effectiveness in improving athletic performance and muscle growth. Some key factors driving this demand include:
-
Rising Awareness of Fitness and Health: Increasing awareness of the benefits of physical fitness and healthy living, especially among the younger population, has significantly raised the consumption of sports supplements.
-
Growth in the Sports Industry: The growing popularity of fitness regimes, bodybuilding, weightlifting, and high-intensity interval training (HIIT) has directly led to increased demand for creatine monohydrate as part of athletes’ supplement routines.
-
Expanding Use in Non-Athletic Populations: Besides athletes and bodybuilders, creatine has gained popularity among older adults seeking cognitive health benefits, as it is believed to support brain function and energy metabolism.
-
Widespread Availability: As e-commerce grows, creatine supplements are becoming easily accessible worldwide. The growth of online retail platforms and specialized sports nutrition stores has also expanded the reach of these products.
-
Rising Disposable Incomes: Economic growth and increased disposable income in developing countries have led to more people investing in sports supplements, including creatine, for improved physical performance.
-
Demand for Clean and Natural Products: With growing concerns about the safety of additives and chemicals, consumers are gravitating toward supplements that offer purity and natural ingredients, creating a demand for creatine monohydrate that is free from artificial additives and fillers.
The global demand for creatine supplements is expected to continue growing, driven by a combination of health trends, growing fitness awareness, and the increasing popularity of sports and fitness activities.
Get a Free Sample Report with Table of Contents@
Raw Materials and Sourcing
To produce Creatine Monohydrate, several raw materials and chemicals are required. The key raw materials include:
-
Creatine (Raw Material): Creatine is the primary ingredient in the manufacturing of creatine monohydrate. It is generally produced synthetically from sarcosine and cyanamide through a chemical reaction. Sarcosine, an intermediate compound, is obtained from amino acids, while cyanamide is synthesized through the reaction of ammonia and carbon.
-
Monohydrate (Water): The term "monohydrate" refers to the fact that the creatine molecule is combined with one molecule of water. During the manufacturing process, the water component is added to the creatine molecule in a controlled reaction to form creatine monohydrate powder.
-
Excipients and Additives: Additional excipients such as stabilizers, anti-caking agents, and flavorings may be used in the formulation process, depending on whether the final product will be in pure creatine form or if flavoring is required (for product variants like flavored creatine powders).
-
Packaging Materials: The final product will need to be packaged in suitable containers such as plastic tubs, pouches, or sachets. Packaging materials should be designed to protect the creatine monohydrate powder from moisture, contamination, and external environmental factors.
The raw materials for manufacturing creatine monohydrate should be sourced from reputable suppliers with strict quality control processes to ensure the highest standards of purity and safety.
Manufacturing Process
The manufacturing of Creatine Monohydrate typically involves several critical steps to convert raw creatine into the final powdered supplement. The process includes:
1. Synthesis of Creatine
The production process begins with the synthesis of creatine from its basic chemical components, sarcosine and cyanamide. This process generally involves a chemical reaction known as the Meyer Process. In this step:
- Sarcosine is mixed with cyanamide under controlled conditions to form creatine.
- The reaction produces creatine in its base form, which is further processed.
2. Crystallization and Hydration
Once the base creatine is synthesized, it is converted into creatine monohydrate. This involves the addition of a controlled amount of water to the creatine, which is then crystallized to form a stable powder. The hydration process ensures the incorporation of water molecules to create creatine monohydrate, which improves its stability and solubility.
- Crystallization is carefully managed to ensure that the water content remains constant and the resulting monohydrate is of high purity.
3. Purification
After crystallization, the product is purified to remove any impurities, unreacted chemicals, or by-products. This is typically done through processes such as:
- Filtration to remove solid impurities.
- Washing to eliminate excess reagents.
- Drying to remove moisture and ensure the powder is free of contaminants.
4. Milling and Grinding
Once purified, the creatine monohydrate crystals are milled into a fine powder. The milling process ensures the powder's uniform particle size, which is important for proper dissolution in water and better bioavailability in the body.
- Milling Equipment: Specialized grinding mills are used to achieve the desired particle size.
- The particle size is controlled to ensure that the powder is easy to dissolve and can be effectively absorbed when consumed.
5. Blending and Mixing (If applicable)
If the creatine monohydrate is to be combined with other ingredients (such as flavoring agents, sweeteners, or other supplements), blending and mixing will be necessary to ensure an even distribution of all components.
This step is important for producing flavored creatine supplements or pre-workout products that combine creatine with other ingredients like caffeine or amino acids.
6. Quality Control Testing
Quality control is a critical aspect of the production process. Various tests are carried out to ensure that the final product is safe, pure, and effective. Some of the key quality control tests include:
- Purity Testing: To ensure that the creatine monohydrate is free from impurities and conforms to the specified standards.
- Microbial Testing: To check for the presence of harmful bacteria or pathogens in the final product.
- Solubility Testing: To ensure that the creatine dissolves properly in water or other liquids.
- Potency Testing: To verify that the creatine is present in the correct concentration to provide the expected performance benefits.
7. Packaging
After passing quality control tests, the creatine monohydrate powder is packaged into suitable containers such as plastic jars, tubs, or pouches. The packaging is labeled with necessary product information, including serving size, nutritional content, and expiration date.
- Packaging Machines: Automated machines are used to fill the containers with the correct amount of creatine monohydrate, seal them, and label them for distribution.
- Labeling and Branding: Accurate labeling is critical for regulatory compliance and for providing consumers with important product information.
Infrastructure and Equipment
Setting up a Creatine Monohydrate Manufacturing Plant requires specialized equipment and infrastructure, including:
1. Manufacturing Equipment
- Synthesis Reactors: For the chemical synthesis of creatine from sarcosine and cyanamide.
- Crystallizers: For the controlled formation of creatine monohydrate crystals.
- Filtration Units: To purify the creatine after synthesis and crystallization.
- Drying Ovens: To remove moisture from the final product and prevent microbial contamination.
- Milling Machines: To grind the creatine monohydrate into a fine powder.
- Blending Machines: For combining creatine with other ingredients (if applicable).
2. Quality Control Laboratories
- Equipped with instruments to carry out purity, potency, solubility, and microbial tests.
3. Packaging Line
- Automated packaging systems to fill, seal, and label the creatine monohydrate containers.
4. Storage Facilities
- Temperature-controlled storage for raw materials and finished products.
Cost Analysis and Financial Planning
Establishing a Creatine Monohydrate Manufacturing Plant involves several significant costs, including:
-
Capital Investment
- Facility Construction: Building a production facility that meets industry standards for hygiene and safety.
- Machinery: Investment in specialized equipment for synthesis, filtration, milling, and packaging.
-
Operating Costs
- Raw Materials: Ongoing procurement of sarcosine, cyanamide, and other excipients.
- Labor: Wages for skilled workers in production, quality control, and packaging.
- Energy: Costs of running energy-intensive machinery.
- Maintenance: Routine maintenance of equipment to ensure smooth operations.
-
Revenue Generation
- Sales: The primary revenue source will come from the sale of creatine monohydrate powders to wholesalers, retailers, and direct-to-consumer platforms.
Regulatory Compliance and Environmental Considerations
Creating a Creatine Monohydrate Manufacturing Plant involves adherence to various regulatory standards:
- Good Manufacturing Practices (GMP): To ensure high-quality production standards.
- Environmental Regulations: Compliance with waste disposal, air quality, and water usage regulations.
- Product Labeling: Accurate labeling in line with regulatory requirements for dietary supplements.
Media Contact
Company Name: Claight Corporation
Contact Person: Lewis Fernandas, Corporate Sales Specialist — U.S.A.
Email: sales@expertmarketresearch.com
Toll Free Number: +1–415–325–5166 | +44–702–402–5790
Address: 30 North Gould Street, Sheridan, WY 82801, USA
Website: www.expertmarketresearch.com
Aus Site: https://www.expertmarketresearch.com.au
- Questions and Answers
- Opinion
- Motivational and Inspiring Story
- Technology
- True & Inspiring Quotes
- Live and Let live
- Focus
- Geopolitics
- Military-Arms/Equipment
- Art
- Causes
- Crafts
- Dance
- Drinks
- Film/Movie
- Fitness
- Food
- Games
- Gardening
- Health
- Home
- Literature
- Music
- Networking
- Other
- Party
- Religion
- Shopping
- Sports
- Theater
- Wellness
- News
- Culture