Root Cause Analysis: Understanding, Methods, and Importance
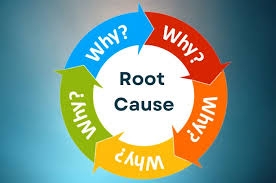
Root Cause Analysis (RCA) is a systematic process used to identify the underlying causes of problems or failures in various systems. It aims to determine the root cause of an issue rather than just addressing its immediate symptoms. RCA is widely used in industries such as manufacturing, healthcare, IT, and business to improve processes, prevent future problems, and ensure operational efficiency.
Importance of Root Cause Analysis
Performing a root cause analysis helps organizations achieve the following:
- Prevent Recurrence: Identifying and addressing the actual cause ensures that the problem does not recur.
- Improve Processes: RCA helps streamline processes and reduce inefficiencies.
- Enhance Safety and Compliance: Identifying potential risks ensures compliance with industry regulations and safety standards.
- Cost Reduction: Preventing recurring problems minimizes operational costs associated with downtime and rework.
- Data-Driven Decision Making: RCA provides actionable insights based on evidence, enabling better decision-making.
Key Steps in Root Cause Analysis
- Define the Problem:
- Clearly describe the issue, including its impact, symptoms, and affected systems or processes.
- Gather Data:
- Collect relevant data about the problem’s occurrence, timeline, and frequency. This may include system logs, performance metrics, or user feedback.
- Identify Possible Causes:
- Brainstorm possible causes by analyzing the collected data and understanding the relationships between contributing factors.
- Analyze and Identify Root Cause:
- Use systematic techniques such as 5 Whys, Fishbone Diagrams, or Fault Tree Analysis to determine the root cause.
- Develop and Implement Solutions:
- Create corrective actions that address the root cause, ensuring that the solution is sustainable.
- Monitor and Evaluate:
- Assess the effectiveness of implemented solutions to confirm that the problem has been resolved.
Popular Methods of Root Cause Analysis
1. 5 Whys Analysis
A simple but effective technique where the question “Why?” is repeatedly asked until the root cause is identified.
Example:
- Problem: Customer complaints about delayed product deliveries.
- Why 1: Delivery team received orders late.
- Why 2: Orders were processed late.
- Why 3: Production delays occurred.
- Why 4: Raw materials were not delivered on time.
- Why 5: Supplier contract was not reviewed effectively.
- Root Cause: Inefficient supplier contract management.
2. Fishbone Diagram (Ishikawa Diagram)
This visual tool categorizes potential causes of a problem into different categories, such as People, Process, Equipment, and Environment.
Use Case: Best suited for complex problems where multiple factors may contribute to the issue.
3. Fault Tree Analysis (FTA)
A top-down, deductive analysis method that maps out potential failure causes using a tree diagram.
Use Case: Ideal for analyzing system-level failures and ensuring compliance in safety-critical industries.
4. Pareto Analysis
Based on the 80/20 rule, this method identifies the most significant factors contributing to a problem.
Use Case: Useful for prioritizing issues and focusing resources on the highest-impact causes.
Applications of Root Cause Analysis
- Manufacturing: Identifying equipment failures and improving production efficiency.
- Healthcare: Investigating medical errors and ensuring patient safety.
- IT and Software Development: Diagnosing system outages, software bugs, and cybersecurity breaches.
- Business and Operations: Enhancing customer satisfaction and optimizing business processes.
Challenges in Conducting Root Cause Analysis
- Inadequate Data Collection: Poor documentation can hinder accurate analysis.
- Bias in Analysis: Confirmation bias may lead to incorrect assumptions.
- Time Constraints: Thorough RCA requires sufficient time, which may not always be feasible.
- Lack of Expertise: Ineffective RCA processes due to lack of trained personnel.
Best Practices for Effective RCA
- Involve Cross-Functional Teams: Engage stakeholders from different departments for a holistic view.
- Use Multiple RCA Techniques: Combining different methods improves accuracy.
- Document Findings: Maintain records of identified causes, solutions, and outcomes.
- Conduct Regular Reviews: Periodically evaluate processes to prevent future occurrences.
Conclusion
Root Cause Analysis is a powerful tool that helps organizations uncover the true reasons behind system failures, enabling them to implement long-lasting solutions. By following a structured approach and applying proven techniques, businesses can improve efficiency, enhance quality, and ensure operational excellence.
- Questions and Answers
- Opinion
- Motivational and Inspiring Story
- Technology
- True & Inspiring Quotes
- Live and Let live
- Focus
- Art
- Causes
- Crafts
- Dance
- Drinks
- Film/Movie
- Fitness
- Food
- الألعاب
- Gardening
- Health
- الرئيسية
- Literature
- Music
- Networking
- أخرى
- Party
- Religion
- Shopping
- Sports
- Theater
- Wellness
- News
- Culture