What makes laser cutting a game-changer in industries like manufacturing and design?
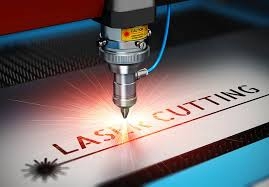
Laser cutting technology has revolutionized industries across the globe, offering an unparalleled combination of precision, speed, and versatility. Whether in manufacturing, automotive, aerospace, or design, laser cutting has emerged as an essential tool that continues to reshape how various sectors approach material processing. This article delves deep into laser cutting technology, its applications, how it’s changing traditional production methods, and the reasons behind its widespread adoption.
What is Laser Cutting?
Laser cutting refers to the process of using a high-powered laser beam to cut through materials. The laser is highly focused and directed onto the surface of the material, causing the material to melt, burn, or vaporize. The precision of the laser ensures that the cut edges are smooth, and minimal material is wasted. This technique can be applied to a variety of materials, including metals, plastics, wood, and even fabrics, making it highly adaptable to a wide range of industries.
The laser cutting process is controlled by a computer numerical control (CNC) system, which allows for incredibly accurate and repeatable cuts. Unlike traditional mechanical cutting methods, where physical contact with the material occurs, laser cutting operates without touching the material. This reduces wear and tear on the cutting tool, allowing for longer service life and less maintenance.
The Role of Laser Cutting in Different Industries
Manufacturing and Fabrication:
Laser cutting has revolutionized the manufacturing industry, particularly in the fabrication of metal parts. The precision of laser cutting allows manufacturers to create intricate designs and tight tolerances, which is crucial in industries that require exact specifications. In the automotive sector, for example, laser cutting plays a key role in producing vehicle components, from chassis parts to body panels, all with exceptional accuracy. The use of laser cutting in sheet metal fabrication has also led to significant cost savings by reducing material waste and improving cutting speed.
Aerospace:
In the aerospace industry, precision and reliability are paramount. Laser cutting technology is used extensively to create critical components for aircraft and spacecraft. The ability to cut through thick metal sheets while maintaining high precision makes laser cutting indispensable in the production of parts that must meet stringent safety standards. For example, turbine blades, wing panels, and engine components are often produced using laser cutting techniques.
Textiles and Fashion Design:
Beyond metalworking, laser cutting has also made its mark in the textile and fashion industries. Designers use lasers to create intricate patterns on fabrics and materials, offering an opportunity for unique and detailed designs that would be time-consuming or impossible with traditional cutting methods. Laser cutting is particularly useful for creating delicate patterns in fabrics such as lace or for producing custom designs in leather goods, upholstery, and accessories.
Electronics:
In the electronics industry, laser cutting plays a critical role in the production of components that require high precision and minimal heat distortion. Laser cutting is used to create circuit boards, microelectronics, and various components that demand tight tolerances. The ability to cut with precision at micro levels makes laser cutting ideal for the intricate work needed in modern electronics manufacturing.
How Laser Cutting Works: Step by Step
-
Laser Generation:
The process begins with a laser generator that produces a high-powered laser beam. This laser beam is typically generated from a gas (such as CO2) or a fiber laser. The laser beam is directed through mirrors or fiber optics to focus on the material to be cut. -
Material Positioning:
Once the laser beam is generated, the material is placed on a work surface. This surface can be flat or 3D, depending on the specific needs of the project. The material is often held in place using clamps or a vacuum system to prevent movement during the cutting process. -
Laser Focus:
The laser beam is focused onto the material using lenses or mirrors. The focal point of the laser beam is extremely concentrated, allowing for precise cutting. Depending on the thickness and type of material, the laser’s focus and intensity can be adjusted to optimize the cutting process. -
Material Interaction:
When the laser hits the material, it heats up the surface, causing the material to melt, burn, or vaporize. In some cases, a jet of gas, such as oxygen or nitrogen, is used to assist in the cutting process. This gas helps to remove the molten material, creating a clean cut and preventing unwanted residue from forming on the edges. -
Cut Completion:
As the laser moves across the material, it continuously cuts along the predefined path. The CNC system guides the laser’s movement with incredible accuracy, creating cuts with tolerances of a fraction of a millimeter. Once the laser completes the cut, the material can be removed from the work surface and is ready for the next stage of production.
Why is Laser Cutting so Popular?
Precision and Accuracy:
One of the standout features of laser cutting is its ability to produce extremely precise cuts. With tolerances often down to a fraction of a millimeter, this level of precision is unmatched by traditional cutting methods. This makes it especially valuable in industries where accuracy is non-negotiable, such as aerospace, electronics, and medical devices.
Speed:
Laser cutting is fast and efficient. The ability to cut through materials at high speeds allows for quicker production times and reduced labor costs. Moreover, the automation of laser cutting systems means that processes can run continuously without human intervention, allowing for high-volume production in industries that require a rapid turnaround.
Flexibility:
Laser cutting works with a wide variety of materials, from metals and plastics to ceramics and composites. This versatility makes it ideal for industries with diverse production needs. Additionally, laser cutting can be used for a variety of applications, such as engraving, etching, and marking, giving it even more flexibility in terms of design.
Minimal Material Waste:
Unlike traditional cutting methods, which often require the use of physical cutting tools, laser cutting produces minimal waste. The precision of the laser means that the cut edges are clean, reducing the amount of material that is wasted during the cutting process. This can result in significant cost savings, especially when working with expensive materials like metals.
No Tool Wear:
Since the laser doesn’t physically touch the material, there is no wear on the cutting tools. Traditional cutting tools, such as blades or saws, require regular maintenance and replacement due to wear. With laser cutting, this issue is eliminated, which leads to lower maintenance costs and less downtime in production.
The Future of Laser Cutting
As industries continue to evolve and demand more precision, the future of laser cutting looks promising. One significant trend is the development of more advanced laser systems that offer even greater power and efficiency. Additionally, the integration of laser cutting with other technologies, such as 3D printing and automation, is expected to create new possibilities in production and design.
Innovations in laser cutting are also being driven by advancements in material science. New materials, such as advanced composites and ultra-hard metals, are being developed that will require even more precise and specialized laser cutting techniques. As technology progresses, laser cutting will continue to play a key role in manufacturing, design, and beyond.
Final Thoughts
Laser cutting has proven itself as a game-changer across various industries, from manufacturing to design. Its unparalleled precision, speed, and versatility make it a cornerstone technology in sectors ranging from aerospace to textiles. As industries continue to demand higher precision and greater efficiency, the role of laser cutting will only expand, making it an invaluable tool in modern production processes. Whether you’re in the automotive, electronics, or fashion industries, embracing laser cutting technology is essential for staying competitive in an increasingly fast-paced and precision-driven market.
- Questions and Answers
- Opinion
- Motivational and Inspiring Story
- Technology
- True & Inspiring Quotes
- Live and Let live
- Art
- Causes
- Crafts
- Dance
- Drinks
- Film/Movie
- Fitness
- Food
- Игры
- Gardening
- Health
- Главная
- Literature
- Music
- Networking
- Другое
- Party
- Religion
- Shopping
- Sports
- Theater
- Wellness
- News
- Culture
- Military Equipments