Engineering Better Flow Paths in Round Drain Baskets Moulds to Reduce Resin Consumption
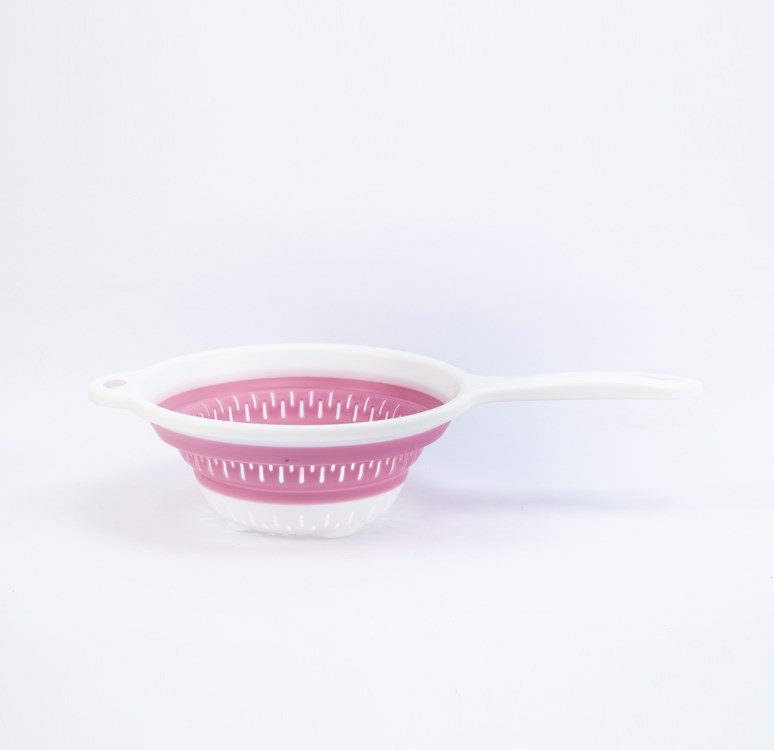
In the injection molding industry, the design of the runner system plays a critical role not only in determining the quality of the molded part but also in the efficiency and sustainability of the entire process. For Round Drain Baskets Moulds, which are typically used to manufacture lightweight, perforated, and functional plastic products, the optimization of runner design is especially important due to the potential for significant material waste. These moulds often produce high-volume items, so even minor inefficiencies in runner layout can lead to large-scale resin loss over time.
One of the first steps in optimizing the runner system in Round Drain Baskets Moulds is analyzing the part geometry and identifying the ideal gating locations. Improper gate placement can cause uneven flow, leading to overpacking, excess flash, or incomplete filling, which in turn contributes to higher reject rates and regrind waste. By positioning gates symmetrically or at points that balance flow around the circular structure of the basket, material usage can be minimized while maintaining part integrity. This is particularly important for the fine mesh areas, where precise fill is necessary but overfilling can cause deformation and unnecessary material buildup.
Another major contributor to material waste in Round Drain Baskets Moulds is the use of overly large or improperly sized runners. Runners that are too large increase the volume of plastic required for each shot, with much of that material never becoming part of the final product. To reduce this, cold runner systems should be carefully balanced and narrowed where possible without compromising flow pressure or fill time. For thin-walled, lightweight items such as drain baskets, reducing the runner cross-section even slightly across thousands of cycles can lead to substantial material savings.
An even more advanced solution is the implementation of hot runner systems in Round Drain Baskets Moulds. Unlike cold runners, which result in solidified plastic that must be trimmed and either discarded or recycled, hot runners maintain the material in a molten state, eliminating solid runner waste. Though the initial cost of hot runner systems can be higher, they often pay for themselves quickly in high-volume production by dramatically reducing material waste and cycle time. Additionally, hot runners can improve surface finish and reduce flow marks in delicate mesh sections by delivering molten resin with more uniform pressure and temperature.
Balanced runner design is another crucial factor in reducing waste. For Round Drain Baskets Moulds, achieving equal flow to multiple cavities—especially in multi-cavity systems—is essential. Unbalanced flow can result in overfilling some parts and underfilling others, leading to more scrap. Flow simulation software is a powerful tool that enables mold designers to visualize and fine-tune runner geometry before production begins. These simulations can highlight areas where pressure drops, flow hesitations, or material surges are likely to occur, allowing for targeted adjustments that improve efficiency and reduce unnecessary material use.
Beyond the physical structure of the runners, material type and processing conditions also influence how efficiently the system operates. Some resins are more sensitive to shear and temperature variation, which can affect flow behavior and increase the likelihood of defects or waste. Choosing appropriate processing temperatures, mold surface finishes, and injection speeds all contribute to maximizing the effective use of material in Round Drain Baskets Moulds.
In addition to the technical benefits, optimizing the runner design in Round Drain Baskets Moulds supports environmental and economic goals. Reduced material waste means lower raw material costs and less energy spent on producing and recycling unused plastic. For manufacturers aiming to meet sustainability targets, this kind of process optimization aligns with broader corporate and regulatory expectations.
Name: Round Drain Baskets Moulds
Mould material: S136
Mould base: P20 steel
Cavity NO: 1+1
Product material: PP+TPR
Runner: Hot/cold
Mould life: 1 million~3 million shots
Delivery time: 35~50 days
- Questions and Answers
- Opinion
- Motivational and Inspiring Story
- Technology
- True & Inspiring Quotes
- Live and Let live
- Art
- Causes
- Crafts
- Dance
- Drinks
- Film/Movie
- Fitness
- Food
- Παιχνίδια
- Gardening
- Health
- Κεντρική Σελίδα
- Literature
- Music
- Networking
- άλλο
- Party
- Religion
- Shopping
- Sports
- Theater
- Wellness
- News
- Culture
- Military Equipments