Kunliwelding’s ER5356 Wire Powers High-Speed Robotic TIG Systems
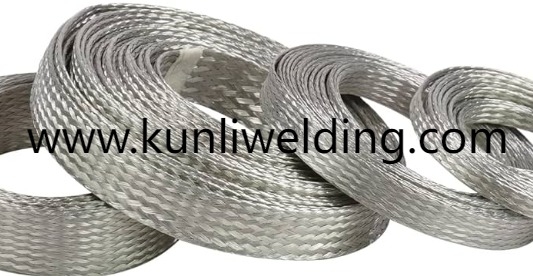
As manufacturers ramp up automated production lines, Aluminum Welding Wire ER5356 has emerged as a dependable choice for robotic TIG and MIG systems. Its balanced magnesium content and consistent feed characteristics ensure stable arcs during high-speed operations, supporting precise fusion on thin panels and complex joint geometries. This seamless compatibility with automated torches boosts throughput and maintains weld quality even under continuous duty cycles.
Robotic cells equipped with vision sensors and adaptive path programming rely on filler metals that tolerate rapid acceleration and deceleration. Wires with fine-tuned surface coatings glide through feed drives without birdnesting, reducing downtime for maintenance and reel changes. Integrators appreciate that ER5356 offers predictable deposition rates and minimal spatter, which translates into fewer touch-up steps and more reliable first-pass yields on battery housings, heat exchangers, and chassis frames.
The ongoing shift toward electric mobility highlights the importance of reproducible welds in critical applications. Battery enclosure seams and body-in-white assemblies demand joints that resist fatigue and galvanic corrosion. ER5356’s corrosion resistance and good mechanical properties in welded zones provide engineers with confidence to specify aluminum across vital vehicle structures. When paired with coordinated parameter databases, welding robots deliver uniform penetration and consistent bead appearance, reinforcing assembly integrity.
Automation also extends to mixed-material joins, where aluminum parts meet high-strength steel components. Transition layers created with ER5356 cushion thermal mismatches and prevent burn-through on thin aluminum sections. Integrated arc pulsation modes in advanced power sources complement the wire’s chemistry, shaping the weld pool for improved control in tight spaces. This synergy between consumable and equipment accelerates cycle times while safeguarding part finishes.
Beyond automotive, industries such as aerospace and marine fabrication leverage automated welding for high-volume assemblies. Long, uninterrupted runs require wires that resist oxidation during storage and maintain straightness on spools. ER5356 wires aged under controlled humidity conditions feed smoothly into robotic torches, helping large-scale operations meet demanding production schedules. Maintenance teams benefit from fewer feed-path blockages and cleaner tip surfaces.
Supply chain resilience has become a priority as global logistics face uncertainties. Manufacturers partnering with reliable suppliers secure local stocking hubs, ensuring just-in-time deliveries of specific wire diameters. Real-time inventory portals allow production planners to track consumption rates and trigger reorder alerts, minimizing the risk of cell stoppages. This collaboration between fabricators and suppliers underpins continuous manufacturing in volatile market conditions.
Training remains vital even in automated environments. Application engineers conduct virtual and on-site workshops, demonstrating optimal parameter settings for ER5356 under various joint designs. They guide technicians through feeder tension adjustments, shielding-gas flow optimization, and pulse waveform selection. These interactive sessions bridge the gap between material science and robotic programming, ensuring that teams harness the wire’s full potential.
Environmental considerations also influence welding operations. As production facilities pursue energy efficiency, minimizing rework and scrap aligns with sustainability goals. ER5356’s reliable fusion properties contribute to less material waste, while advanced melting practices at wire mills reduce carbon footprints. Fabricators can showcase eco-credentials alongside automated capabilities, demonstrating their commitment to greener manufacturing.
Innovation in filler metal development continues to address automation challenges. Research into microalloying elements and refined grain structures seeks to further improve crack resistance and mechanical strength. As robotics evolve with machine-learning algorithms, future welding cells will adapt in real time to subtle variations in wire feed or joint fit-up, maintaining optimal weld conditions without human intervention.
For engineers and production managers exploring automation-ready welding consumables, detailed specifications and expert support are available at www.kunliwelding.com .
- Questions and Answers
- Opinion
- Motivational and Inspiring Story
- Technology
- True & Inspiring Quotes
- Live and Let live
- Focus
- Geopolitics
- Military-Arms/Equipment
- Sécurité
- Economy/Economic
- Art
- Causes
- Crafts
- Dance
- Drinks
- Film/Movie
- Fitness
- Food
- Jeux
- Gardening
- Health
- Domicile
- Literature
- Music
- Networking
- Autre
- Party
- Religion
- Shopping
- Sports
- Theater
- Health and Wellness
- News
- Culture