How to Optimize Your CNC Boring Operations for Faster Production
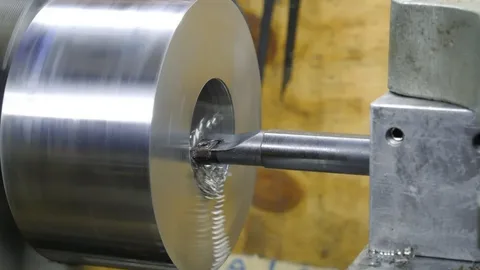
CNC boring operations are crucial in industries that require high-precision machining, particularly in sectors like aerospace, automotive, and manufacturing. Optimizing these operations can significantly improve production efficiency, reduce operational costs, and ensure the highest quality of finished products. In this article, we’ll explore practical strategies to optimize CNC boring operations, focusing on techniques to boost production speed while maintaining precision.
Choose the Right Tools for Efficient CNC Boring Operations
Selecting the right tools is foundational to optimizing CNC boring operations. Tool selection directly impacts the speed, accuracy, and surface finish of your work. The tool’s material and geometry play a major role; for instance, carbide tools are preferred for high-speed machining due to their durability and resistance to wear. Using adjustable boring heads with fine-tuning capabilities also allows operators to achieve precise measurements and avoid the need for multiple passes, reducing cycle time.
Additionally, using vibration-dampening tool holders can further enhance tool life and improve surface quality by minimizing chatter during boring operations. When operators choose tools optimized for their material type and machining conditions, CNC boring operations can run smoother, faster, and more efficiently, leading to reduced downtime and fewer tool replacements.
Optimize CNC Machine Parameters for Speed and Precision
Machine parameters such as feed rate, spindle speed, and depth of cut must be carefully optimized for effective CNC boring operations. Higher spindle speeds can increase production rates, but they also raise the risk of tool wear if not balanced with appropriate feed rates. Lower feed rates, while typically safer, can slow production. Striking a balance between these two is key to maintaining both speed and tool longevity. Operators should use high-speed machining techniques, adjusting parameters based on the tool's material and the specific requirements of the boring task.
Furthermore, taking advantage of the CNC machine’s built-in capabilities, such as adaptive control and high-speed machining modes, can significantly improve boring operations. Adaptive control allows the machine to adjust parameters based on real-time feedback, optimizing cutting conditions as they change throughout the operation. This not only speeds up production but also ensures consistent quality, even with variations in material hardness or tool wear.
Implement Effective Coolant Strategies for Better Boring Efficiency
Coolants play a critical role in CNC boring operations by helping control heat generation and prolonging tool life. An effective coolant strategy can reduce friction and wear, enabling faster machining speeds. Flood coolant, mist coolant, and high-pressure coolant systems are common approaches. For CNC boring operations, high-pressure coolant systems are often recommended as they provide consistent cooling and efficiently remove chips, reducing the risk of tool clogging and damage.
In addition to coolant type, positioning and flow rate are also important factors. Proper coolant flow to the cutting edge ensures even heat dissipation, minimizing thermal expansion that can affect bore dimensions. Regular monitoring and adjustment of coolant flow can further optimize production speed and prevent overheating issues that might lead to tool failure or degraded quality. By investing in an optimal coolant system, operators can increase the lifespan of cutting tools and enhance overall productivity in CNC boring operations.
Utilize Automation and Monitoring for Consistent Production
Automation and real-time monitoring systems can greatly enhance CNC boring operations. Automated tool changers, for example, allow machines to switch between tools rapidly, reducing downtime and ensuring continuous production. By pre-programming tool change cycles based on expected tool wear, operators can maintain high production rates with minimal manual intervention. Additionally, automated quality control systems with sensors can monitor dimensions, reducing errors and improving consistency.
Moreover, real-time monitoring systems help track machine and tool performance, providing data on spindle speed, feed rate, and other parameters. This data enables operators to identify any deviations from optimal conditions and make adjustments immediately. Predictive maintenance can also be implemented, scheduling repairs or replacements before breakdowns occur, which helps minimize unexpected downtime. Together, automation and monitoring technologies allow for efficient, uninterrupted CNC boring operations, thereby enhancing productivity and precision.
Regularly Maintain and Calibrate CNC Machines for Peak Performance
Maintenance is key to ensuring that CNC machines operate at optimal levels, especially in high-precision boring operations. Regular maintenance, including cleaning, lubrication, and calibration, prevents wear and tear on components that could otherwise impact machine accuracy and speed. Regularly inspecting machine alignment and recalibrating axis controls can correct minor errors, ensuring that each boring operation meets stringent tolerance requirements.
Calibrating CNC machines is especially crucial in CNC boring operations, where even minor inaccuracies can lead to significant issues in production. Using laser alignment and probing systems to verify machine accuracy allows operators to make fine adjustments that maintain dimensional integrity. Scheduled maintenance checks and calibrations not only extend the life of the machine but also sustain higher production rates, as well-maintained equipment operates more reliably and consistently.
Conclusion
Optimizing CNC boring operations requires a multifaceted approach, from selecting the appropriate tools and machine parameters to implementing effective coolant strategies, automation, and maintenance. By focusing on these key aspects, manufacturers can significantly enhance production speed, reduce operational costs, and ensure consistent quality in CNC boring processes.
- Questions and Answers
- Opinion
- Motivational and Inspiring Story
- Technology
- True & Inspiring Quotes
- Live and Let live
- Focus
- Art
- Causes
- Crafts
- Dance
- Drinks
- Film/Movie
- Fitness
- Food
- Games
- Gardening
- Health
- Home
- Literature
- Music
- Networking
- Other
- Party
- Religion
- Shopping
- Sports
- Theater
- Wellness
- News
- Culture