A Deep Dive into the Manufacturing Processes of Tin Packaging
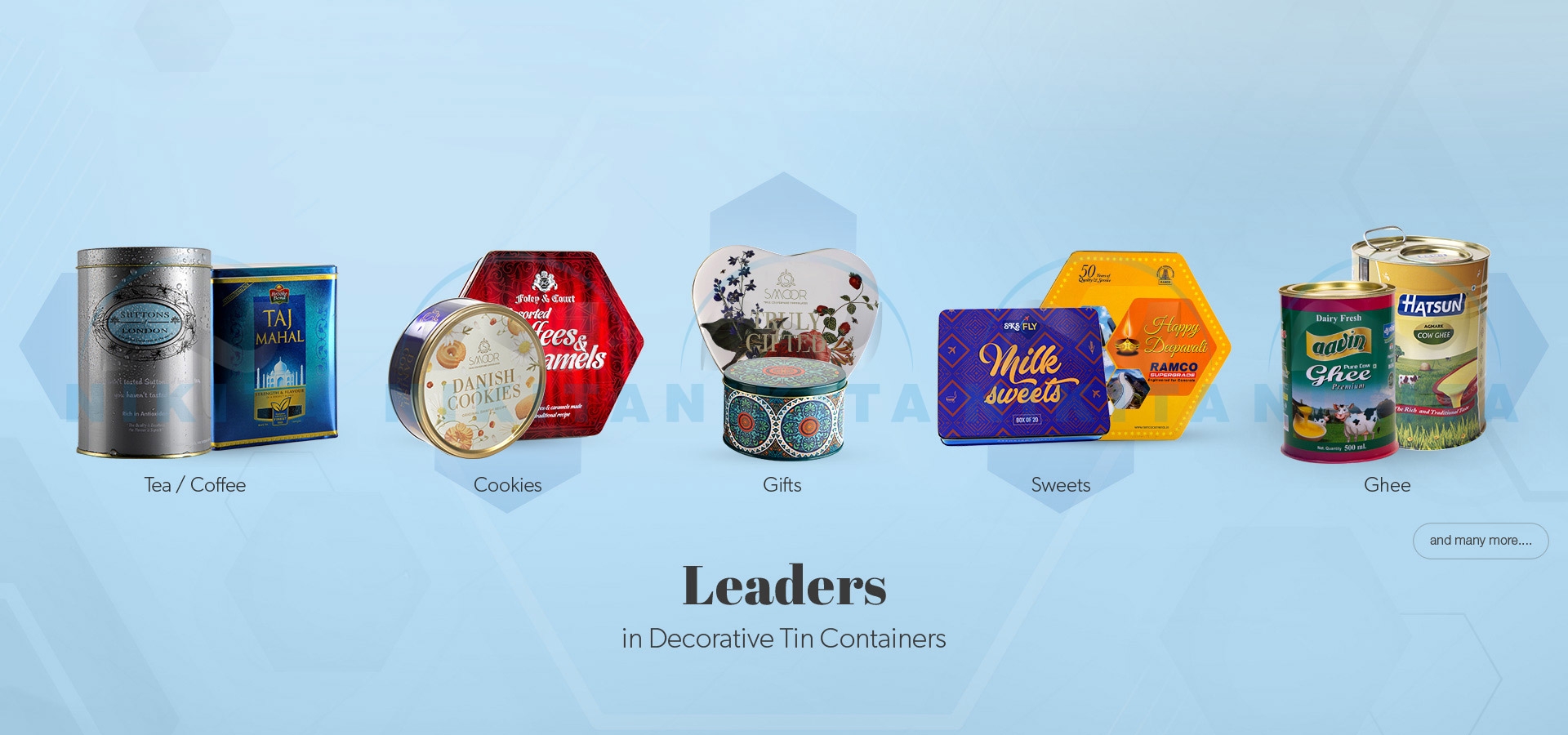
Tin packaging is widely used across industries due to its durability, aesthetic appeal, and eco-friendly nature. Behind every can, box, or container lies a highly specialized manufacturing process that transforms raw materials into the finished product that protects, preserves, and enhances the items inside. In this blog, we will take a deep dive into the manufacturing processes of tin packaging, exploring the steps involved, the technology used, and the quality control measures that ensure every package meets the highest standards.
1. The Basics of Tin Packaging Production
The production of tin packaging begins with the raw material—tinplate. Tinplate is a thin steel sheet coated with a layer of tin, which provides the corrosion resistance and appearance needed for packaging. Tin is preferred because of its strength, recyclability, and ability to protect products from contaminants. The first step in the manufacturing process is sourcing high-quality steel and tin that meet industry standards.
Once the steel sheets are ready, they undergo several processes to transform them into functional and attractive packaging. These processes are carried out by tin packaging manufacturers using specialized equipment to ensure precise production and consistent results.
2. Step 1: Blanking and Cutting
The manufacturing process begins with blanking, where large rolls of tinplate are unwound and cut into flat sheets. These sheets are then cut into smaller pieces, or blanks, that are the basic shape and size of the final package. The blanking process requires high precision, as the dimensions of each blank must be accurate to ensure that the final packaging fits together properly during the subsequent steps.
The tin packaging manufacturers use automated cutting machines to ensure that the blanks are consistent in size and shape, which reduces material waste and enhances production efficiency. Additionally, modern technologies like laser cutting can provide even greater accuracy and flexibility when designing custom packaging shapes.
3. Step 2: Deep Drawing or Stamping
After the blanks are prepared, the next step is deep drawing or stamping. This is the process where the flat blanks are transformed into three-dimensional shapes, such as cans, boxes, or other containers. The blanks are placed into a mold and then pressed by a hydraulic press to create a deep, formed shape. The mold determines the final shape and size of the packaging, which can range from simple cylindrical cans to intricate custom shapes used for high-end packaging.
In the case of tin packaging manufacturers creating cans, the deep drawing process results in a seamless container, where the sides are drawn up into shape and the bottom is attached. For other packaging types, such as decorative boxes or specialized containers, stamping and pressing help create the desired structure.
4. Step 3: Trimming and Seaming
Once the containers are formed, the edges of the packaging need to be trimmed to ensure smooth, clean finishes. This step removes any excess material from the top, bottom, or sides of the containers that may have been left over from the forming process.
Seaming is the next critical step, especially for products like food cans, where airtight sealing is necessary. In this process, the top and bottom of the tin packaging are attached to the body of the container. The seams are formed by folding the edges and crimping them together, creating a durable, leak-proof seal. In the case of food and beverage cans, this step is particularly important as it ensures the product is securely enclosed and preserved.
5. Step 4: Coating and Decoration
The next phase in the tin packaging manufacturing process involves coating and decorating the packaging. The interior of the tin is coated with a protective layer to prevent corrosion from moisture, air, or the product itself. This coating is crucial in industries like food packaging, where moisture can cause rust and spoilage.
On the exterior, tin packaging manufacturers often apply decorative coatings to enhance the visual appeal of the packaging. There are various ways to decorate tin packaging, such as printing, embossing, and applying finishes. Printing can include everything from simple logos to detailed, full-color designs. Advanced techniques like lithographic printing allow for high-quality, vibrant graphics, while embossing creates raised patterns or text that adds texture and depth to the packaging.
The choice of coating and decoration is influenced by the type of product being packaged. For instance, products like food and beverages require coatings that ensure product safety, while cosmetics or luxury goods benefit from elegant, eye-catching designs.
6. Step 5: Drying and Curing
After the coatings are applied, the tin packaging enters the drying and curing process. This step involves heating the packages in ovens to harden the protective coatings and allow them to bond securely to the surface of the tin. For decorative finishes, curing ensures that the print or design remains intact and resistant to smudging or fading.
The curing process also helps to ensure the longevity of the packaging, preventing the coatings from peeling or chipping. Tin packaging manufacturers carefully control the temperature and duration of this step to avoid any damage to the packaging while ensuring optimal results.
7. Step 6: Quality Control and Inspection
Quality control is an essential part of the tin packaging manufacturing process. After the containers are coated and decorated, they undergo rigorous inspection to ensure that they meet safety, durability, and aesthetic standards. Automated and manual inspections are used to check for defects such as dents, scratches, uneven coatings, or improperly sealed seams.
Tin packaging manufacturers utilize advanced technologies, such as x-ray inspection and automated vision systems, to detect even the smallest defects in the packaging. This step helps ensure that the final product is safe for use, meets industry standards, and is free from manufacturing errors that could compromise the product inside.
In addition to physical inspections, manufacturers also conduct tests to check the packaging’s performance under different conditions. For example, pressure tests are done to ensure that cans can withstand the rigors of transportation and handling, while durability tests verify that the packaging remains intact during storage and use.
8. Step 7: Final Assembly and Packaging
After all quality checks are completed, the final step in the process is assembly and packaging. At this stage, the individual pieces are ready to be shipped out for filling and distribution. Depending on the design, tin packaging may also be fitted with additional components such as lids, labels, or handles.
For products like food cans, the packaging is often sent to food processing plants where it is filled with the product and sealed. For other products, such as cosmetics or luxury goods, the packaging is often ready to be sent to retailers or directly to consumers.
Conclusion
The manufacturing process of tin packaging is a complex and highly specialized procedure that combines advanced technology, precision engineering, and creative design. From blanking and deep drawing to coating, decorating, and quality control, every step is critical to ensuring the final product is durable, visually appealing, and ready to protect its contents.
By working with experienced tin packaging manufacturers, businesses can ensure that they receive high-quality packaging that meets the specific needs of their products while providing optimal protection and an attractive presentation. With a focus on sustainability, innovation, and design, the manufacturing processes behind tin packaging continue to evolve, making it an increasingly popular choice for a wide range of industries.
- Questions and Answers
- Opinion
- Motivational and Inspiring Story
- Technology
- True & Inspiring Quotes
- Live and Let live
- Focus
- Art
- Causes
- Crafts
- Dance
- Drinks
- Film/Movie
- Fitness
- Food
- Spiele
- Gardening
- Health
- Startseite
- Literature
- Music
- Networking
- Andere
- Party
- Religion
- Shopping
- Sports
- Theater
- Wellness
- News
- Culture