Pressure Gauge Calibration: Ensuring Accurate Measurements
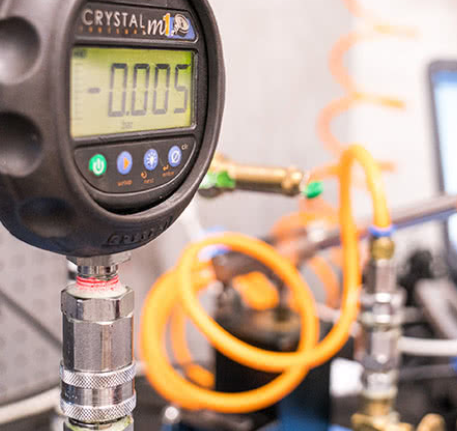
Pressure gauge calibration is a vital process in industries that rely on precise pressure measurements to ensure safety, efficiency, and compliance. From manufacturing to healthcare, calibrated pressure gauges play a critical role in maintaining operational integrity.
What is Pressure Gauge Calibration?
Pressure gauge calibration is the process of verifying and adjusting the accuracy of a pressure gauge by comparing its measurements against a standard reference. This ensures the gauge provides reliable readings that align with industry standards and requirements.
Why is Pressure Gauge Calibration Important?
- Safety Assurance: Accurate pressure readings are crucial to preventing equipment failures or accidents caused by overpressure or underpressure.
- Operational Efficiency: Properly calibrated gauges help optimize system performance and reduce energy consumption by maintaining correct pressure levels.
- Regulatory Compliance: Many industries, including oil and gas, pharmaceuticals, and food processing, require calibration to meet strict regulatory standards.
- Cost Savings: Avoiding inaccuracies reduces waste, minimizes downtime, and extends the lifespan of equipment.
The Calibration Process
- Preparation:
- Select a suitable reference standard with known accuracy.
- Isolate the pressure gauge from the system to prevent interference.
- Testing:
- Connect the gauge to a calibration device, such as a deadweight tester or a pressure calibrator.
- Apply incremental pressure levels and record the gauge readings against the reference standard.
- Adjustment:
- If discrepancies are detected, adjust the gauge to align with the standard.
- Some gauges allow fine-tuning through mechanical or digital adjustments.
- Documentation:
- Record the calibration results, including date, technician details, and any adjustments made.
- Maintain a calibration certificate for compliance and audit purposes.
Types of Pressure Gauge Calibration
- Deadweight Tester Calibration: Using calibrated weights to generate precise pressure levels, this method is highly accurate and widely used for primary calibration.
- Pneumatic Calibration: Ideal for low-pressure gauges, this method employs compressed air to test and adjust the gauge.
- Hydraulic Calibration: Suitable for high-pressure gauges, this method uses a hydraulic pump to apply pressure.
- Automated Calibration Systems: Advanced systems automate the process, reducing human error and increasing efficiency.
Factors Affecting Calibration
- Environmental Conditions: Temperature, humidity, and vibration can impact calibration accuracy.
- Frequency of Use: Gauges subjected to frequent or extreme pressure variations may require more regular calibration.
- Quality of Equipment: High-quality gauges with robust construction typically maintain accuracy longer than lower-quality alternatives.
- Industry Standards: Adherence to standards like ISO 9001 or ANSI ensures consistent calibration practices.
How Often Should Pressure Gauges be Calibrated?
The calibration frequency depends on several factors:
- Manufacturer Recommendations: Follow the suggested intervals for calibration.
- Industry Requirements: Some sectors mandate specific calibration frequencies.
- Usage Intensity: High-usage gauges may need more frequent checks.
- Historical Data: Analyze past calibration records to determine trends and set appropriate intervals.
Best Practices for Calibration
- Maintain a Schedule: Use a calibration management system to track due dates and ensure timely calibrations.
- Use Certified Equipment: Ensure calibration tools and reference standards are certified and traceable to national or international standards.
- Train Technicians: Employ skilled personnel who understand the nuances of calibration procedures.
- Regularly Inspect Gauges: Perform routine visual inspections to identify wear and tear that might affect accuracy.
Calibration Challenges and Solutions
- Access to Standards:
- Challenge: Limited access to high-accuracy reference standards.
- Solution: Partner with accredited calibration service providers.
- Time Constraints:
- Challenge: Operational downtime during calibration.
- Solution: Use portable calibrators to perform on-site calibrations with minimal disruption.
- Complex Systems:
- Challenge: Calibrating gauges integrated into complex systems.
- Solution: Develop detailed procedures and use advanced calibration tools.
The Future of Pressure Gauge Calibration
- Digital Calibration: Advanced digital gauges with self-calibration features are reducing the need for manual adjustments.
- IoT Integration: Smart pressure gauges connected to IoT platforms enable real-time monitoring and predictive maintenance.
- AI-Powered Analysis: Artificial intelligence is enhancing calibration accuracy by identifying patterns and optimizing procedures.
For more details, visit us:
- Questions and Answers
- Opinion
- Motivational and Inspiring Story
- Technology
- True & Inspiring Quotes
- Live and Let live
- Art
- Causes
- Crafts
- Dance
- Drinks
- Film/Movie
- Fitness
- Food
- Παιχνίδια
- Gardening
- Health
- Κεντρική Σελίδα
- Literature
- Music
- Networking
- άλλο
- Party
- Religion
- Shopping
- Sports
- Theater
- Wellness
- News
- Culture
- Military Equipments